Разрабатываем заклинивший поршень суппорта тормозов
Тормозные механизмы (суппорта) передних колес автомобилей ВАЗ 2108, 2109, 21099 работают в условиях постоянного воздействия внешней агрессивной среды (соль, грязь, вода и пр.). В связи с этим ревизию и обслуживание суппортов и тормозных колодок рекомендуется проводить каждые 15 тысяч км пробега.
Заклинивание или «закисание» поршней в цилиндрах суппортов чаще всего является следствием отсутствия периодического контроля за состоянием тормозных механизмов, повреждении их защитных пыльников, сильном износе тормозных колодок при котором поршни слишком далеко выдвигаются из цилиндров, попадая тем самым под внешнее воздействие, наличием воды или посторонних примесей в тормозной жидкости.
Справка: поршни тормозных механизмов передних колес автомобилей ВАЗ 2108, 2109, 21099 имеют зеркальное покрытие, такое же покрытие имеется внутри цилиндров. В цилиндрах установлены резиновые кольца, возвращающие поршни в исходное состояние после выдвижения.
Снаружи поршни защищены пыльниками (защитными колпачками со стопорными кольцами).
Повреждение зеркального покрытия поршней («закисание») приводит к потере их подвижности в цилиндрах и как следствие к неполному растормаживанию передних колес, так как колодки постоянно прижаты к тормозным дискам. При этом происходит ускоренный износ колодок, перегрев и коробление тормозных дисков, повышается расход топлива, нарушается управляемость автомобиля (уводит в сторону) и его динамика, появляется вибрация и биение при нажатии на педаль тормоза.
Разработать «закисший» поршень можно как минимум двумя способами:
— без демонтажа тормозного механизма с автомобиля;
— на снятом тормозном механизме.
В первом случае необходимо поддомкратить автомобиль, снять колесо, очистить суппорт от грязи снаружи, отсоединить и поднять его плавующую скобу.
Поднимаем плавающую скобу суппорта и очищаем тормозной цилиндр hr>
Снимаем стопорное кольцо и пыльник цилиндра, удаляем из под него грязь при помощи тряпки, смоченной бензином и жесткой кисти или зубной щетки. Слегка нажимаем на педаль тормоза, чтобы поршень немного (максимум сантиметр) выдвинулся из цилиндра. Еще раз производим очистку, стараясь не повредить зеркало поршня и удалить только грязь и отложения. Наждачной бумагой зачищать поршень нельзя, так как можно повредить зеркало. Народный способ очистки отложений – применение шершавого деревянного бруска, который снимет отложение и не повредит цилиндр. Снимаем крышку с бачка тормозной жидкости и при помощи разводного ключа или тисков утапливаем поршень обратно в цилиндр. Жмем на педаль тормоза, выдвигая поршень, и опять утапливаем его. Проводим такую процедуру разработки его подвижности раз 20-30. После чего наносим графитную смазку на выступающую часть поршня, устанавливаем новый пыльник и стопорное кольцо.
Плюс этого способа — нет необходимости сливать тормозную жидкость из контуров тормозной системы автомобиля и прокачивать тормоза.
Во втором случае снимаем тормозной цилиндр и проводим его разборку и разработку. Этот способ подойдет при капитальной ревизии суппортов, так как необходимо либо сливать тормозную жидкость, либо глушить тормозную трубку, что все-равно чревато потерей некоторого количества жидкости и подразумевает проведения прокачки тормозов после выполнения работ.
Поршень из цилиндра необходимо выдавить либо еще до его снятия (нажав на педаль тормоза), либо на уже снятом поршне подать воздух под давлением в отверстие под тормозную трубку. Перед выдавливанием снимаем с поршня стопорное кольцо и пыльник. Извлеченный поршень стараемся не поцарапать. Очищаем его от загрязнений и окислений способом описанным выше, если необходимо меняем резиновое уплотнительное кольцо, промываем и продуваем цилиндр. Перед сборкой смазываем тормозной жидкостью внутри тормозного цилиндра, сам поршень смазываем графитной смазкой. Вдавливаем его вовнутрь цилиндра (например, при помощи тисков), одеваем сверху новый пыльник и стопорное кольцо.
Все перечисленные выше манипуляции имеют смысл лишь при незначительном повреждении поршня или цилиндра. В случае полного заклинивания поршня и невозможности его разработки следует заменить тормозной цилиндр с поршнем.
Примечания и дополнения
— После разработки поршней тормозных цилиндров передних колес автомобиля необходимо смазать направляющие пальцы.
Еще статьи по тормозной системе автомобилей ВАЗ 2108, 2109, 21099
— Проверка и регулировка свободного хода педали тормоза автомобилей ВАЗ 2108, 2109, 21099
— Проверка тормозной системы автомобилей ВАЗ 2108, 2109, 21099
— Схема стояночной тормозной системы автомобилей ВАЗ 2108, 2109, 21099
— Схема рабочей тормозной системы автомобилей ВАЗ 2108, 2109, 21099
— Замена передних тормозных колодок на автомобилях ВАЗ 2108, 2109, 21099
— Замена задних тормозных колодок на автомобилях ВАЗ 2108, 2109, 21099
Подписывайтесь на нас!
Ремонт тормозных суппортов своими руками: инструкция
В большинстве современных автомобилей применяются тормоза дискового типа. Главным рабочим органом служит суппорт, который зажимает диск при помощи колодок. Чтобы данная система работала с высокой эффективностью, необходим регулярный контроль технического состояния. Для этого вы можете обратиться на наш автосервис, чтобы там провели профессиональную диагностику, а при необходимости и ремонтные работы.
Кроме профилактики и ремонта есть возможность заказать ремкомплекты суппортов для автомобилей следующих производителей: ВАЗ, Opel, Ford, Audi, Renault, Peugeot, Citroen, Mazda, Mitsubishi, Volkswagen, BMW и других. Но многие автовладельцы предпочитают выполнять данные процедуры своими силами. Чтобы отремонтировать тормозной суппорт самостоятельно, нет необходимости в специальных условиях. Достаточно лишь набора стандартного слесарного инструмента и устройства, с помощью которого можно надежно поддомкратить авто.
Признаки неисправного суппорта
Основные признаки неисправности:
- увеличенный тормозной путь;
- затрудненный накат;
- машину уводит в сторону при торможении;
- вибрация педали при торможении;
- скрежет в районе суппорта при движении:
стоит отметить, что причины могут быть разные, от попавшего камня до банального износа колодок, однако износ колодок может быть вызван неисправным суппортом; - характерные следы перегрева на тормозном диске;
- неравномерный износ колодок из одного суппорта;
- чрезмерный нагрев диска.
Причины поломки суппорта
Основные причины неисправности:
- поврежденные направляющие;
- грязь на рабочей поверхности свободного хода колодок;
- износ манжеты;
- потеря герметичности пыльника поршня.
Стоит отметить, что некоторые автолюбители решают не проводить восстановления тормозного суппорта, а производят замену. Но в большинстве случаев вполне можно обойтись переборкой и приобретением ремонтного комплекта, чем значительно сэкономить.
Описание процесса ремонта тормозной системы
Необходимо поддомкратить авто, чтобы иметь возможность демонтировать необходимое колесо. Дальше нужно осмотреть колодки, определив уровень и равномерность их износа. После следует отсоединить суппорт от скобы и визуально осмотреть пыльник поршня на предмет повреждений. У поршня должен быть легкий ход, при его вдавливании в корпус. Бывает так, что даже за целым, на первый взгляд, пыльником скрывается грязь и влага, а соответственно и ржавчина.
Поэтому стоит заглянуть под пыльник, аккуратно воспользовавшись инструментом. Поверхность поршня должна быть чистой и ровной. Если какой-либо из данных дефектов обнаружится, то суппорт нуждается в разборке и восстановлении при помощи ремкомплекта. Кроме этого необходимо проверить состояние направляющих и мест соприкосновения колодок для свободного хода.
Разборка тормозного суппорта:
- Произвести отсоединение тормозной шланги от суппорта. Для предотвращения потери жидкости, следует передавить шланг или закупорить отверстие.
- Снять пыльник поршня.
- Далее произвести извлечение поршня из корпуса суппорта.
- Удаление старой манжеты.
- Очищение места посадки пыльника, а также канавки манжеты.
- Промывка всего узла в целом и чистыми руками произвести
- Установка манжеты, смазанной тормозной жидкостью, в посадочную канавку.
- Установка очищенного либо нового поршня. Производится вертикально, равномерным воздействием руками.
- Надевание пыльника в середине пути поршня.
- После входа поршня в корпус, следует снова его немного выдвинуть, например воздухом. Такая процедура поможет убедиться, что пыльник сел ровно и не получил повреждений.
- Утопленный поршень снова может быть готов к процессу установки.
Стоит также не забывать о прокачке контура, который подвергался утечке жидкости.
Ремонт тормозных суппортов своими руками легко выполнить с элементарными слесарными навыками. Главное, не забывать о внимательности и тщательно выполнять все описанные нюансы работы. Ведь тормозная система – это залог безопасного передвижения автомобиля.
Проектирование для аддитивного производства тормозного суппорта с оптимизированной топологией с помощью систематического подхода на основе платформы САПР
Резюме
был выполнен процесс оптимизации конструкции переднего тормозного суппорта Formula SAE, который будет напечатан методом порошковой сварки (PBF). DfAM заключается в использовании титанового сплава Ti6Al4V для лучшей стойкости к высоким температурам и оптимизированной топологии формы, позволяющей снизить вес, несмотря на увеличение плотности. Были обсуждены структурные и тепловые характеристики. Методы, специфичные для процесса DfAM, были реализованы для внутренних геометрических элементов и оптимизированных форм. Представлен дизайн для аддитивного рабочего процесса и, наконец, синтезирован использованный подход к проектированию, основанный на платформе САПР.
Ключевые слова
- DfAM
- Оптимизация топологии
- Платформа CAD
- Тормозной суппорт
- Автомобильная промышленность
Скачать документ конференции в формате PDF
1 Введение
Поскольку внедрение аддитивного производства (AM) дает большие возможности во многих промышленных условиях, особенно тех, которые сосредоточены на высокопроизводительных компонентах, изучение методологий DfAM становится фундаментальным [1]. Как показано в предыдущей работе авторов [2], рабочий процесс разработки оптимизированных компонентов для производства с помощью АП не всегда эффективен. Была определена общая структура, состоящая из задач, которые необходимо выполнить от определения концепции до функциональных частей конечного использования (рис. 1).
Основные операции, составляющие рабочий процесс, описаны ниже. Планирование продукта — это начальная фаза. На этом этапе проводится анализ деталей и сборок вместе с определением целей и ограничений для сбора всех входных данных о продукте и определения списка требований.
Рис. 1.Рабочий процесс для аддитивного производства [2].
Полноразмерное изображение
Этап проектирования представляет собой итеративную доработку моделей с целью оптимизации продукта. Этап индустриализации — это шаг, необходимый для создания надежного производства деталей и оптимизации процесса. Наконец, производство охватывает процесс печати деталей с соответствующими операциями постобработки и контроля. Внедрение интегрированных платформ на основе САПР в качестве базового инструмента для ускорения рабочего процесса и повышения его эффективности обсуждалось авторами [2]. Представленная работа направлена на подробное описание методологического подхода, ориентированного на этап проектирования (оптимизация продукта) на основе оптимизации топологии. Тормозной суппорт гоночного автомобиля был переработан для производства методом селективного лазерного плавления (SLM) AM с целью повышения производительности за счет применения подхода на основе платформы САПР. Итеративное усовершенствование проекта, необходимое для получения окончательных моделей и технической документации продукта (TPD), описывается в реальном приложении, и анализируется подход DfAM.
2 Метод
Как показано на рис. 2, этап проектирования основан на последовательности задач, краткое изложение которых приведено ниже. CAD-моделирование Design Space (DS) и Non-Design Space (NDS) является обязательным для подготовки геометрии с учетом проектных ограничений.
Этап проектирования.
Полноразмерное изображение
Оптимизация топологии (ТО) — это задача вычисления формы детали в соответствии с настройками алгоритма цели и ограничениями. Для получения оптимизированной модели детали требуется интерпретация / уточнение проекта САПР, и можно использовать как автоматические инструменты (A-CAD), так и ручную реконструкцию геометрии (CAD). Моделирование продукта (ProdSIM) — это задача проверки оптимизированных деталей в отношении целей проектирования и ограничений. Циклы повторного проектирования необходимы для оптимизации дизайна.
3 Практический пример
Компоненты гоночных автомобилей обычно подвергаются комбинированным нагрузкам, и в частности тормозные системы могут иметь проблемы в эксплуатации, так как им приходится работать с интенсивными нагрузками при высоких температурах [3]. Коммерческий тормозной суппорт Formula SAE, первоначально изготовленный путем фрезерования на станке с ЧПУ из алюминиевого сплава Ergal 7075-T6, достиг температуры, близкой к 300 ° C, с проблемами прочности и деформации, поэтому он был переработан для печати с помощью процесса SLM. Сержент и др. анализы [4] показывают критические условия для рабочего тормозного суппорта с точки зрения конструкции и то, как оптимизация топологии позволяет улучшить его характеристики. Трави Фариас и др. работа [5] показывает, насколько принципиальной является терморегуляция, поскольку при высоких температурах механические свойства материалов ухудшаются. Более того, в исследовании утверждается, что аддитивное моделирование позволяет конструировать сложные геометрические формы, которые могут увеличить отношение поверхности к объему модели и облегчить рассеивание тепла. Полностью разработанный корпус Bugatti [6] демонстрирует с помощью экспериментальных испытаний возможность использования титановых сплавов и приводит к повышению производительности. Тем не менее, ни один из этих случаев не основан на комплексном подходе к проектированию, возможные возможности которого обсуждались авторами [2]. Ссылаясь на рабочий процесс, изображенный на рис. 1, теперь описаны задачи планирования и проектирования продукта.
Все задачи выполняются на платформе Dassault Systèmes 3DExperience CAD [7] для интегрированного проектирования продуктов и процессов.
3.1 Планирование продукта
Анализ коммерческого компонента является отправной точкой DfAM с целью определения конструктивных особенностей, обеспечивающих одинаковое рабочее поведение. В частности, это касается в большей степени гидродинамики масляных каналов. Кроме того, этап принятия решения о покупке/производстве приводит к сохранению стандартных и коммерческих элементов оригинальной детали, в то время как корпус и поршни переделываются. Поскольку исходный 2D-чертеж недоступен, функциональные характеристики были измерены метрологическим оборудованием для определения допусков муфты. Данные о механических и тепловых нагрузках, действующих на деталь, были собраны с помощью экспериментальных измерений и аналитических моделей динамики транспортного средства. Максимальное давление в масляном контуре составляет 100 бар, а тангенциальная нагрузка для максимального тормозного момента на дисковом тормозе составляет 14 кН. Температуры достигают в среднем около 200 °C с максимальными пиками, близкими к 300 °C. Был проведен анализ сборки группы передних колес, чтобы определить физические конструктивные ограничения, связанные с подгонкой деталей, соединением и работой. Основываясь на этом наборе данных, МКЭ исходного суппорта возвращает конструкционные цели проекта, такие как повышение жесткости при высоких температурах и снижение веса. Фундаментальным шагом является выбор материала в соответствии с таблицами данных, относящимися к SLM. Поскольку механические свойства сплава 7075-Т6 значительно ухудшаются при высокой температуре, был выбран титановый сплав Ti6Al4V. Согласно литературным данным, по сравнению со сплавом 7075-Т6, он имеет при рабочей температуре примерно на 11 % более высокое отношение модуля Юнга к плотности и даже на 45 % более высокое отношение предела текучести к плотности. Кроме того, требуется производственный анализ с механической обработкой, удельной теплоемкостью и обработкой поверхности.
Данные о продуктах собираются в Списке требований. Цели DfAM заключаются в использовании Ti6Al4V для лучшей устойчивости к высоким температурам и оптимизированной топологии формы для снижения веса. Открытая и разветвленная геометрия также может увеличить соотношение поверхность/объем с преимуществами для управления тепловым режимом с точки зрения рассеивания тепла.
3.2 Проектирование
Начальным этапом этапа проектирования является моделирование DS. Он начинается с входных данных анализа деталей и сборок, чтобы определить максимальный объем, доступный для расчета ТО. Большинство функциональных элементов следует удалить, в то время как элементы для соединения деталей и основных муфт должны быть сохранены (поршни, тормозные колодки и кожухи пальцев, отверстия для болтов, крышки суппортов), чтобы ограничить область. Требуются также радиус обода колеса, обременение поворотного кулака и тормозного диска или траектории сборки деталей. Объемы NDS должны быть определены для вставки областей для сохранения материала, например, отверстий под болты или внутренних элементов.
Вторым шагом является настройка модели FE для проведения оптимизации и анализа. Для винтов применяются шарнирные ограничители. Максимальная тангенциальная нагрузка 14 кН (от тормозного момента) приложена к узлу, надетому на среднюю плоскость дискового тормоза, соединенному с контактными поверхностями (RBE3) тормозных колодок. Максимальное давление масла 100 бар приложено к внутренним поверхностям корпусов поршней, а эквивалентные расчетные реактивные силы 9,8 кН приложены к участкам резьбы крышек суппортов. Материал создается с использованием параметров направления сборки (из-за анизотропии сплава AM [8]) в пользу безопасности. Дискретизация расчетного пространства производится сеткой тетраэдра 1,5 мм (TL4) и уточнениями. Выполняется предварительный статический анализ расчетного пространства для проверки настройки модели и проверки ее жесткости (идеальное максимальное значение). ТО настраивается на снижение массы мишени и минимизацию податливости.
Выполняется концептуальное итеративное исследование проекта с изучением ограничений симметрии и уточнением расчетов. Эта геометрия делает правую и левую части одинаковыми и сокращает моделирование до половины тела с потенциальными преимуществами времени и затрат на проектирование и производство. Результаты используются для создания твердотельных моделей посредством улучшенного сглаживания концептуальной генерации форм. Они видят непосредственно ProdSIM от FEA, показывая, что асимметричная плоскость конструкции обеспечивает лучшую производительность с точки зрения максимального смещения. На рис. 3 показаны результаты TO C1 и C2.
Слева направо: концептуальные результаты (C1, C2) и проекты (V1, V2, V3).
Изображение в натуральную величину
После завершения ТО начинается итеративный проект по улучшению формы детали. Происходит интерпретация дизайна, моделирующая функциональную геометрию с дизайном поверхности и разветвленную форму с дизайном свободной формы. Кроме того, масляные каналы введены и используются для повышения жесткости деталей, воздействуя на их форму и положение. ProdSIM с помощью FEA необходим для прогнозирования деформации и напряжения детали. Последние два цикла уточнения включают детальное проектирование каждой детали корпуса (прокладки, уплотнительные кольца, клапаны, штифты) и реализацию рекомендаций DfAM для внутренних характеристик (самонесущие поперечные сечения каналов) и разветвленных форм (толщина, поддерживающая углы), в соответствии с ориентацией деталей, запланированной для строительства. После проверки результаты производственного анализа используются для создания модели необработанной детали и окончательных чертежей (TPD).
4 Результаты и обсуждение
Для проверки статической нагрузки учитывается предел текучести при 220 °C со значением для направления сборки (Z) и дополнительным коэффициентом безопасности 1,2 (применение в гонках), таким образом, рассчитывается допустимое напряжение 560 МПа. На рис. 4 показаны результаты. Кроме того, необходимо сделать замечание по усталостной долговечности и надлежащей обработке на напряженных участках [9].
Смещение и напряжение V1, V2 и V3.
Изображение в полный размер
Как видно из таблицы 1, максимальное смещение при 220 °C составляет 0,675 мм для исходного суппорта и 0,614 мм для окончательной конструкции оптимизированного (9% снижения), в то время как масса тела увеличивается с 248 г до 184 г (экономия 25,8%). Более того, аналитическое термическое исследование цикла торможения по коду Matlab показывает снижение рабочих температур на 20 °C для окончательной конструкции. Последнее замечание заключается в том, что титан имеет наихудшие трибологические характеристики (низкая износостойкость и высокая склонность к размеру), и поэтому для обработки поверхности поршней используется химическое никелирование (Niplate). Пересчитаны холодные и горячие допуски для муфт.
Таблица 1. Сравнение конструкций.Полноразмерная таблица
Итеративное усовершенствование проекта теперь синтезировано. Циклы оптимизации продукта, каждый из которых выполняется в интегрированной CAD-платформе, могут быть описаны на разных уровнях. Первый цикл включает в себя оптимизацию топологии, A-CAD и моделирование продукта и создает концептуальные решения (C1, C2). Используются автоматические инструменты для интерпретации проекта, а циклы создаются быстро благодаря интегрированной платформе. Второй цикл включает в себя САПР и моделирование продукта и позволяет разрабатывать варианты воплощения (V1) или окончательные (V2, V3) с добавлением элементов рабочего проекта. Проектирование требует ручной (трудоемкой) интерпретации геометрии только для первой итерации, в то время как повторное проектирование чрезвычайно облегчается интегрированной средой для последующих.
Ссылки
Кумке, М., Вачке, Х., Виетор, Т.: Новая методологическая основа проектирования для аддитивного производства. Виртуальный физ. Прототипирование 11 (1), 3–19 (2016)
CrossRef Google ученый
«>Limpert, R.: Brake Design and Safety, S.A.E. Международный, США (1999)
Google ученый
Сержент Н., Тирович М., Воверис Дж.: Оптимизация конструкции тормозного суппорта с оппозитным поршнем. англ. Оптим. 14 (11), 1520–1537 (2014)
CrossRef Google ученый
Трави Фариас, Л., Шоммер, А., Циглер Хазелейн, Б., Ноймайер, Г., Коста де Оливейра, Л., Солиман, П., Уолтер, Р.: Проектирование тормозного суппорта с использованием топологии Оптимизация интегрирована с прямым лазерным спеканием металла. С.А.Е. Международный (2015)
Google ученый
«>Dassault Systemes. https://www.3ds.com/about-3ds/3dexperience-platform/. Доступ 01 2020
Симонелли, М., Це, Ю.Ю., Так, К.: Влияние ориентации сборки на механические свойства и режимы разрушения SLM Ti6Al4V. Матер. науч. англ. 616 , 1–11 (2014)
Google ученый
Денти, Л., Бассоли, Э., Гатто, А., Сантеккья, Э., Менгуччи, П.: Усталостная долговечность и микроструктура Ti6Al4V, изготовленного присадкой, после различных процессов отделки. Матер. науч. англ. 755 , 1–9 (2019)
Google ученый
Далпадуло, Э., Пини, Ф., Леали, Ф.: Оценка дизайна для аддитивного производства на основе CAD-платформ. средства и методы проектирования в промышленной инженерии. В: Материалы ADM 2019, стр. 970–981 (2020)
Google ученый
Wischeropp, T.M., Hoch, H., Beckmann, F., Emmelmann, C.: Возможности тормозной технологии благодаря аддитивному производству на примере тормозного суппорта Bugatti. В: ХХXVII. Internationales μ-Symposium 2018 Bremsen-Fachtagung, стр. 181–19.3 (2019)
Google ученый
Скачать ссылки
Информация об авторе
Авторы и организации
Инженерный факультет «Энцо Феррари», Университет Модены и Реджо-Эмилии, Via Vivaricelli 10/1, 400uliculic90, Mode04, Италия Фабио Пини и Франческо Леали
Авторы
- Энрико Далпадуло Посмотреть публикации автора
Вы также можете искать этого автора в PubMed Google Scholar
- Fabio Pini
Просмотр публикаций автора
Вы также можете искать этого автора в PubMed Google Scholar
- Francesco Leali
Просмотр публикаций автора
Вы также можете искать этого автора в PubMed Google Scholar
Автор, ответственный за переписку
Соответствие
Фабио Пини.
Информация о редакторе
Редакторы и принадлежность
ИНСТИТУТ ARTS ET Métiers, AIX EN PROVENCE CEDEX 1, France
Lionel Roucoules
INSA Toulous Compiègne, Compiegne Cedex, France
Benoit Eynard
Departamento de Mecánica, Universidad de Navarra, Сан-Себастьян-Доностия, Гипускоа, Испания
Д-р Паз Морер Камо
Кафедра управленческой информации и технологии производства, Университет Бергамо, Бергамо, Италия
Проф. Катерина Рицци
Права и разрешения
Доступ открыт по лицензии2 условия международной лицензии Creative Commons Attribution 4.0 (http://creativecommons.org/licenses/by/4.0/), которая разрешает использование, совместное использование, адаптацию, распространение и воспроизведение на любом носителе или в любом формате, если вы предоставляете соответствующие укажите автора (авторов) и источник, предоставьте ссылку на лицензию Creative Commons и укажите, были ли внесены изменения.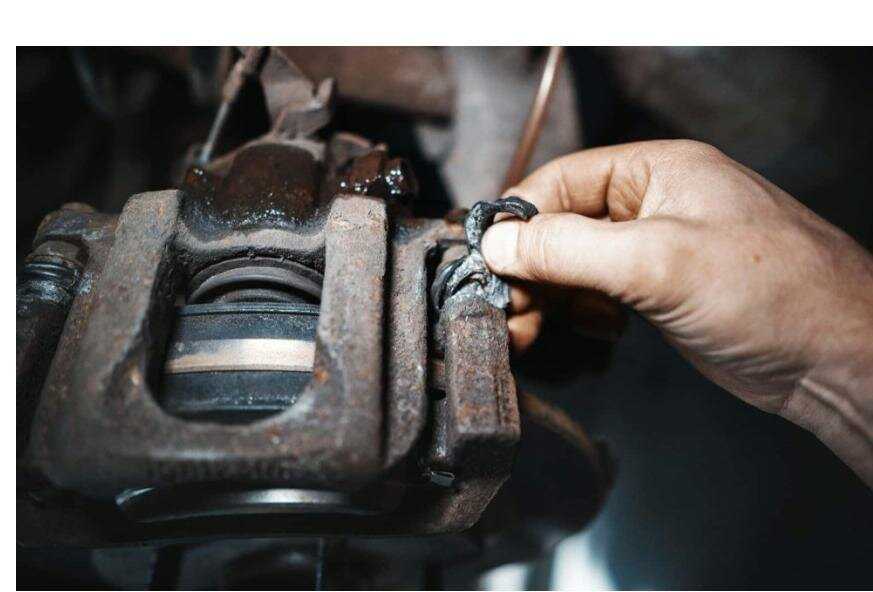
Изображения или другие сторонние материалы в этой главе включены в лицензию Creative Commons главы, если иное не указано в кредитной строке материала. Если материал не включен в лицензию Creative Commons главы, а предполагаемое использование вами не разрешено законом или выходит за рамки разрешенного использования, вам необходимо получить разрешение непосредственно от владельца авторских прав.
Перепечатка и разрешения
Информация об авторских правах
© 2021 Автор(ы)
Об этой статье
Дизайны тормозных суппортов, темы, шаблоны и графические элементы, загружаемые на Dribbble
Просмотр значка дискового тормоза
Значок дискового тормоза
Посмотреть обновление логотипа Carmmunity 2019 [до и после]
Обновление логотипа Carmmunity, 2019 г. [До и после]
Просмотр Детали велосипеда — шатун, каретка, тормозные диски
Велосипедные детали — кривошип, каретка, тормозные диски
Просмотр значка приложения для переоборудования автомобиля.
Значок приложения для переоборудования автомобиля.
Просмотр пунктирных значков: запасные части для велосипедов
Точечные значки: запасные части для велосипедов
Посмотреть логотип дискового тормоза
Логотип дискового тормоза
Посмотреть Колесо Времени
Колесо Времени
Посмотреть дизайн фирменного стиля Monogram GA
Фирменный дизайн с монограммой GA
Посмотреть Хот Вилс
Хот Вилс
Просмотр значков автосервиса
Значки автосервиса
Посмотреть тормоз
Посмотреть штангенциркуль
Штангенциркуль
Посмотреть велосипедные стоп-сигналы
Велосипедные стоп-сигналы
Посмотреть WIP тормозного диска
Тормозной диск WIP
Посмотреть иллюстрацию EA 2
EA Artwork 2
Просмотр строительных и строительных иконок
Строительные иконки
Посмотреть автозапчасти
Автозапчасти
Посмотреть Onward Automotive Co.