Антикор для скрытых полостей Dinitrol Penetrant LT и открытой поверхности кузова 1 л
- Описание
- Характеристики
Предназначен для порогов, лонжеронов и рамы. Инновационный антикоррозионный состав, предназначенный для обработки открытых поверхностей и труднодоступных полостей. Состоит из минеральных восков, растворителей и уникальных ингибиторов коррозии. Содержащиеся растворители в процессе высыхания состава после нанесения испаряются, в результате чего формируется воскообразная пленка с водоотталкивающими свойствами.
Хорошо противостоит коррозии и замедляет развитие имеющихся очагов ржавчины. Готовое покрытие имеет бежевый цвет. Имеет исключительную степень защиты после нанесения. Наносить материал необходимо при помощи воздушного пистолета-распылителя с компрессором. Описание продукта
Антикор Dinitrol Penetrant LT для полостей – это инновационный антикоррозионный состав, предназначенный для обработки открытых поверхностей и труднодоступных полостей.
Средство Dinitrol Penetrant LT от коррозии состоит из минеральных восков, растворителей и уникальных ингибиторов коррозии. Содержащиеся растворители в процессе высыхания состава после нанесения испаряются, в результате чего формируется воскообразная пленка с водоотталкивающими свойствами. Хорошо противостоит коррозии и замедляет развитие имеющихся очагов ржавчины. Готовое покрытие имеет бежевый цвет.
Динитрол Penetrant LT. Область использования
Применять Dinitrol Penetrant LT можно для обработки скрытых полостей, доступ к которым затруднен:
внутренности порогов;
двери;
усилители кузова и пр.
Подобные скрытые места есть в каждом автомобиле, и именно здесь нередко начинают образовываться коррозионные очаги.
Антикор подходит для обработки деталей и поверхностей новых и подержанных транспортных средств.
Динитрол Penetrant LT. Способ применения
Наносить Dinitrol Penetrant LT можно при помощи пистолета-распылителя, подключенного к компрессорному оборудованию. Давление используется от 5 барр наносить нужно равномерно на расстоянии 30 см от обрабатываемой поверхности.
Постарайтесь максимально очистить рабочие места от загрязнений и высушить их, что повысить адгезию состава. Если есть ржавчина, то её нужно зачистить и обработать преобразователем ржавчины RC800 или полностью зачистить до металла и для лучшего эффекта обработать антигравийным покрытием, и после этого положить слой антикора тогда защитная пленка не даст распространятся коррозии дальше так как доступ к кислороду будет заблокирован антикором.
Очень хорошо этим средством обрабатывать скрытые части порогов, состав образует воскообразную пленку с водоотталкивающими свойствами и со временем не будет высыхать и трескаться, тем самым надолго защитит внутреннюю часть порога от воздействия окружающей среды и коррозии. Так же материал широко применяют в обработке лонжеронов и рамы особенно внутренних их частей и полостей.
Для лучшего эффекта защиты можно применить дополнительный слой антикора в качестве второго слоя. В зависимости от обрабатываемой поверхности, разные материалы можно использовать. Для днища это динитрол 482, Metallic а для арок может еще и подойти динитрол CAR. Каждый слой увеличивает гарантию и повышает степень защиты от коррозии и воздействия солевых реагентов от дорог и внешней окружающей среды.
- Артикул: 016646
- Базовая единица: шт
- Производитель: Dinitrol
- Модель производителя: Penetrant LT
- Объем тары, фасовка, л: 1
- Артикул производителя: 11080
Производитель оставляет за собой право на изменение внешнего вида, комплектации и технических характеристик товара Антикор для скрытых полостей Dinitrol Penetrant LT и открытой поверхности кузова 1 л без уведомления дилеров. Указанная информация не является публичной офертой.
Антикор авто
Единые телефоны Антикор — центров:
+7 495 661-2440
+7 495 505-2668
+7 800 222-2640
Антикоррозионные материалы
Цены
• Подготовка (разборка, мойка, осмотр, сушка, зачистка, маскировка)
• Обработка скрытых полостей нижней части — основания кузова (лонжероны, пороги, усилители пола, швы, полые кронштейны подвески, поперечные балки)
• Обработка днища, колесных арок (покрытие днища, колесных арок, антигравий, «жидкие подкрылки»)
• Обработка скрытых полостей верхней части кузова (двери, стойки, усилители капота, багажника, швы, уплотнители, молдинги)
• Сборка, мойка (контроль покрытия, снятие маскировки, установка снятых деталей, удаление попавших на ЛКП антикоррозионных материалов, финальная мойка кузова, протирка стекол)
1. Подготовка
— Автомобиль устанавливается на подъемник, снимаются колеса,
— демонтируются подкрылки, брызговики, защитные кожухи…
— Кузов тщательно промывается водой под высоким давлением…
— затем, наносятся моечные растворы…
— выдержав некоторое время, чтобы дать химии поработать, растворы смываются…
— В процессе антикоррозионной обработки, подготовка это одна из важнейших (и наиболее длительных по времени) составляющих, поэтому мойке уделяется большое внимание.
— Отдельно моются кожухи, подкрылки и т. д.
— Затем кузов сушится. Чаше это делается с применением тепловых пушек.
Например, при использовании тепловых пушек мощностью 25 -30 кВт, и потоком воздуха около 3000 куб.
Перед сушкой нужно убедиться, что с дренажных отверстий удалены заглушки.
— в процессе сушки, кузов также продувается сжатым воздухом.
Это делается с целью ускорения процесса сушки, а также что бы выгнать воду из швов, пазух, карманов и дополнительной прочистки труднодоступных мест, которые не промылись при мойке.
— просушенный кузов тщательно осматривается для определения состояния защитных покрытий и общего состояния кузова (наличие коррозии, деформаций, повреждений, отслоений защитных и декоративных покрытий и т. д.)
…визуально…
…, с помощью бороскопа…
— Далее укрываются детали, не подлежащие обработке (тормозные механизмы, двигатель, выхлопная система, некоторые элементы подвески…)
При маскировке нужно обратить внимание на датчики АБС, кислородные датчики на выпускной системе, радиаторы, различные электрические разъемы.
2. Обработка скрытых полостей основания
образец схемы обработки (PDF формат)
Определяются точки обработки (на большинство автомобилей существуют рекомендованные производителем схемы обработки с указанием точек распыления)
— Снимаются резиновые, пластиковые заглушки, в некоторых случаях, при невозможности доступа через существующие отверстия, сверлятся дополнительные отверстия, при сверлении необходимо использовать специальные сверла, которые не дают стружки, могущей попасть внутрь детали.
— Далее обрабатываются скрытые полости основания кузова (пороги, лонжероны, поперечные балки, полые кронштейны подвески, усилители пола,…).
Антикоррозийная обработка скрытых полостей автомобиля производится, так называемым МЛ-методом: внутрь детали вводится специальная насадка и под давлением распыляются МЛ материалы: проникающие составы, пропитывающие сварные швы и формирующие на внутренней поверхности детали защитную пленку.
3. Обработка днища и арок колёс
Далее производится нанесение износоусточивых покрытий, так называемые «жидкие подкрылки», на подверженные абразивному воздействию детали (колесные арки, нижние полки лонжеронов, нижние продольные швы порогов и т. д.)
Основной слой наносится либо распылителем, либо кистью или шпателем, а затем подравнивается распылителем, для получения более гладкой поверхности.
В некоторых случаях, на лицевые поверхности наносят полимерные защитные материалы, так называемый «антигравий»
Далее производится антикоррозийная обработка днища автомобиля. Чаще всего, материалы на днище наносят безвоздушным распылением, под высоким давлением. В антикор центрах, для обработки днища применяют насосы с пневмоприводом, для высоковязких материалов, с коэффициентами гидравлического усиления 26-50 единиц, что позволяет создать давление на выходе (в форсунке распылителя) до 400 атмосфер.
Иногда, поверхности днища, колесных арок покрывают теми же МЛ-материалами, которыми обрабатываются скрытые полости. Такая обработка очень эффективна, но недолговечна, МЛ составы имеют невысокую механическую прочность и, грубо говоря, «смываются» с днища. Это делается в случаях, когда кузов имеет серьезные коррозионные повреждения (послойная, сквозная коррозия) и есть сомнения, что удастся подготовить поверхности для нанесения полноценных долговременных покрытий.
— устанавливаются на место подкрылки, кожухи, брызговики…
— снимается маскировка…
— устанавливаются на место колеса…
— Машина опускается на пол для проведения антикоррозийной обработки скрытых полостей верха кузова (стойки, двери, усилители капота, багажника, швы и усилители моторного отсека, уплотнители…)
— Из машины вытаскивается все лишнее….
— Для предотвращения попадания материалов на обивки салона, сиденья, переднюю панель, салон укрывается чехлами
4. Обработка скрытых полостей верха кузова
Далее, используя различные насадки (МЛ-метод) обрабатываются полые детали верхней части кузова (двери, стойки, усилители капота, багажника, уплотнители, швы и усилители моторного отсека, молдинги,…)
— усилители капота…
— коробчатые, полые профили, швы и усилители моторного отсека…
— уплотнители, молдинги…
— усилители крышки багажника…
— швы, полые профили, усилители багажного отсека…
— стойки, двери, уплотнители…
5. Сборка и удаление попавших на кузов антикоррозионных материалов
— Устанавливаются на место снятые заглушки, концевые выключатели, в случае сверления дополнительных отверстий, они закрываются резиновыми пробками.
— Проверяется плотность посадки резиновых уплотнителей проемов дверей, багажника, удаляются оставшиеся маскировочные материалы.
— кузов протирается специальным раствором от попавших на кузов материалов, возможно удаление, попавших на лакокрасочное покрытие антикоров уайт-спиритом. Не рекомендуется применение сильных растворителей.
— оформляется сертификат, с указанием даты, фамилий мастеров, использованных материалов, периодичностью гарантийных осмотров, рекомендаций.
6. Эксплуатация автомобиля после обработки
— После обработки желательно не ездить на машине в течение нескольких часов.
— Далее, в течение суток положен щадящий режим эксплуатации.
— Рекомендуется избегать высоких скоростей, езды по грунтовым дорогам, буксования, при проезде луж нужно снижать скорость.
— Два-три дня не рекомендуется мыть машину.
-Так же после обработки в течение пары недель, желательно, не мыть днище, арки под высоким давлением.
ЦЕНЫ на наши услуги
наверх страницы
cоставлено: Антикор.рф, г. Москва.
Возврат к списку услуг
что это такое и как это происходит
Металл, из которого изготовлен кузов автомобиля, под воздействием влажности, перепадов температур начинает ржаветь с момента его изготовления. Вибрация возникает при эксплуатации автомобиля. Слой краски и изоляционного материала в некоторых местах немного отслоился от поверхности металла. Там будет образовываться конденсат, создавая условия, способствующие ржавчине. Со временем на стыках деталей и швах появится желтое пятно, явный признак коррозии. Чтобы свести этот процесс к минимуму, на кузовные и днищевые детали наносится антикоррозионное покрытие.
Чем обрабатывают автомобиль от коррозии?
Виды антикоррозионного покрытия:
- Битумная мастика защищает и консервирует металл.
- Средство от ржавчины на масляной основе создает после высыхания защитную пленку.
- Антикоррозийный состав с парафином эластичный и долговечный.
- Продукт на основе каучука с высокой степенью сцепления с металлической поверхностью.
- Жидкий пластик является вспомогательной защитой, так как имеет низкую износостойкость.
Как происходит антикоррозийная обработка автомобиля?
На СТО автомобили утепляются с помощью специального оборудования. Общий порядок работ:
- Машину загоняют на лифте, снимают защиту пластика снизу. Осмотрите арки и раму, если она есть.
- Составляется карта ржавчины, т.е. определяются места, где есть коррозия, для последующей усиленной обработки этих поверхностей.
- Составляют заказ и заполняют документы, указывая перечень работ.
- Автомобиль моется и сушится струей горячего воздуха. Обрабатывать машину лучше в жаркую погоду, тогда сушка занимает около полутора часов, зимой – час-полтора.
Поверхности обезжириваются.
- Все застежки и кромки покрыты утеплителем, например, быстросохнущим воском.
- Антикоррозийный состав распыляется во все полости по периметру автомобиля. Также желательно лечить скрытые полости. Для этого нужно сверлить отверстия. Если ваш автомобиль на гарантии, вам не следует этого делать.
- Продуйте сжатым воздухом днище и колесные арки, чтобы удалить старую мастику, пыль и остатки воды.
- Наносится грунтовка, затем наносится антикоррозийное покрытие.
- Места с сильной коррозией тщательно очищаются. Эта процедура стоит недешево. Если бюджет ограничен, то можно остановить коррозию кузова. Пораженный участок зачищают щеткой и покрывают средством от ржавчины – составом, глубоко проникающим в структуру ржавчины и замедляющим ее распространение.
Заводская обработка от коррозии длится около 3 лет или менее. Это зависит от качества металла и того, какой продукт использовался для изоляции поверхностей. Антикоррозийное покрытие на новом автомобиле лучше сохранит его первоначальный вид и может предотвратить необходимость дорогостоящего ремонта в будущем.
Особенно важно утеплить днище и полость, так как эти части автомобиля в процессе эксплуатации получают наибольшую нагрузку: пыль, влага, удары камней. Зимой это лед, соль и вещества, посыпанные дорогами, которые разрушают защитный слой. Обрабатывать автомобиль от коррозии рекомендуется один раз в 12-24 месяца.
Стандартные системы защиты от коррозии для зданий
Эта статья предназначена для помощи тем, кто отвечает либо за составление спецификаций по защите от коррозии, либо в качестве подрядчиков, которым необходимо выполнить указанные требования. Предоставленная информация основана на промышленном опыте и представлена в виде текущих практических таблиц «стандартных» систем защиты от коррозии для стальных конструкций в различных средах.
Нанесение покрытий на заводе-изготовителе
(Изображение предоставлено Hempel UK Ltd. )
Содержание
- 1 Введение
- 2 Внутренняя среда
- 2.1 Скрытые стальные конструкции
- 2.2 Видимая стальная конструкция
- 2.3 Плавательные бассейны
- 3 Внешняя среда
- 4 стены по периметру
- 4.1 Стальные конструкции в четком отделении от внешнего листа
- 4.2 Стальные конструкции, соприкасающиеся с внешним листом
- 5 Ссылки
- 6 ресурсов
- 7 Дополнительная литература
- 8 См. также
- 9 Внешние ссылки
- 10 CPD
Введение
Таблицы «стандартных» систем для металлоконструкций, представленные в этой статье, относятся к «категориям окружающей среды», которые основаны на данных BS EN ISO 12944-2 [1] и BS EN ISO 9223 [2] , которые описаны в таблице ниже.
Категория коррозионной активности | Низкоуглеродистая сталь Потеря толщины (мкм) a | Примеры типичных сред (только для информации) | |
---|---|---|---|
Внешний вид | Интерьер | ||
C1 очень низкий | ≤ 1,3 | — | Отапливаемые здания с чистой атмосферой, напр.![]() |
C2 низкий | > 1,3 до 25 | Атмосферы с низким уровнем загрязнения: преимущественно сельские районы | Неотапливаемые здания, в которых может образовываться конденсат, напр. склады, спортивные залы |
C3 средний | > 25 до 50 | Городская и промышленная атмосфера, умеренное загрязнение двуокисью серы; прибрежная зона с низкой соленостью | Производственные помещения с повышенной влажностью и некоторым загрязнением воздуха, напр. предприятия пищевой промышленности, прачечные, пивоварни, молокозаводы |
C4 высокий | > от 50 до 80 | Промышленные районы и прибрежные районы с умеренным уровнем засоления | Химические заводы, плавательные бассейны, прибрежные суда и верфи |
C5 очень высокий | > 80 до 200 | Промышленные зоны с повышенной влажностью и агрессивной атмосферой и прибрежные зоны с повышенной соленостью | Здания или зоны с почти постоянной конденсацией и высоким уровнем загрязнения |
CX крайний | > 200 до 700 | Морские районы с высокой соленостью и промышленные районы с экстремальной влажностью и агрессивной атмосферой, субтропической и тропической атмосферой | Промышленные зоны с повышенной влажностью и агрессивной атмосферой |
Примечания:
- 1 мкм (1 микрон) = 0,001 мм
- a Значения потери толщины приведены после первого года воздействия.
Убытки могут уменьшиться в последующие годы.
- Значения потерь, используемые для категорий коррозионной активности, идентичны значениям, указанным в BS EN ISO 9223 [2] .
Во многих случаях стальные конструкции будут находиться в теплом сухом помещении, где они не будут подвергаться коррозии, а структурная устойчивость здания не будет подвергаться угрозе в течение расчетного срока службы (обычно принимается равным 50 годам). В таких условиях (классификация С1) антикоррозионное покрытие не требуется. Примеры включают стальные конструкции внутри сухих зданий с нейтральной атмосферой, таких как многоэтажные офисные здания, магазины, школы, гостиницы, жилые дома, терминалы аэропортов, больницы и т. д.
Однако, когда стальные конструкции подвергаются воздействию влаги, скорость коррозии зависит от жесткости окружающей среды. В таких случаях должна быть предусмотрена система покрытия, соответствующая категории окружающей среды. Обратите внимание, что в некоторых зданиях могут быть зоны, в которых действуют различные условия окружающей среды, например. больницы обычно относятся к категории C1, но могут содержать кухни и прачечные, которые обычно относятся к категории C3. Некоторые типы зданий, такие как автостоянки, могут подпадать под любую из вышеперечисленных категорий или их комбинации в зависимости от их местоположения, дизайна и конструкции. Категории более высокого риска для внутренних помещений (например, C4 и C5) не рассматриваются в этой статье, и пользователям рекомендуется обратиться за советом к специалисту, если их проект связан с такими ситуациями.
Защитные системы в таблицах имеют уникальные идентификаторы. Толщина пленки, указанная в таблицах, является номинальным значением сухой пленки (мкм = микрон = 0,001 мм). В таблицах также указана ближайшая эквивалентная система в BS EN ISO 12944-5 [3] и необходимая подготовка поверхности в соответствии с BS EN ISO 8501-1 [4]
. систем защиты, описанных на этих страницах, расчетный срок службы строительных конструкций принят равным 50 годам.
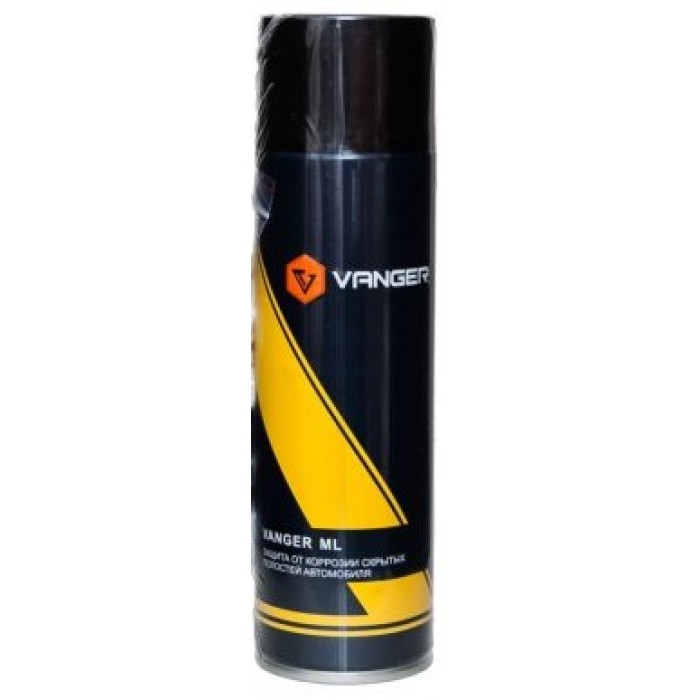
Срок службы конструкции
Период отсутствия сильной коррозии стальных конструкций, которая может привести к ослаблению конструкции. Эта цифра предполагает отсутствие механических повреждений при эксплуатации, техническое обслуживание не проводится и что до 1 мм стали может быть утеряно с поверхности при скорости коррозии для каждой среды, указанной в BS EN ISO 12944-2 [1] . Видимые стальные конструкции, как правило, доступны для обслуживания, а в случае проведения перекраски указанный срок службы конструкции будет продлен.
Срок службы покрытия
Ожидаемый срок эксплуатации защитного покрытия. Более частое повторное покрытие часто может быть предпочтительным по декоративным причинам из-за выцветания, загрязнения, износа и т. Д. Предполагается, что скрытые стальные конструкции недоступны для обслуживания, поэтому показатель срока службы покрытия скрытых систем стальных конструкций неприменим.
[top]Скрытые металлоконструкции
Номер системы | ИХ-С2-А | ИХ-С2-В | ИХ-С2-С |
---|---|---|---|
Срок службы конструкции | 50+ | 50+ | 50+ |
Срок службы покрытия | нет данных | нет данных | н/д |
Ближайший эквивалент BS EN ISO 12944-5 [3] | — | С2.07 | С2.01 или С2.05 |
Подготовка поверхности по BS EN ISO 8501-1 [4] | Ручная очистка до St2 | Пескоструйная очистка до Sa 2½ | Пескоструйная очистка до Sa 2½ |
Заводские покрытия | — | Эпоксидный грунт на основе фосфата цинка (примечание 1) 80 мкм | Акриловый грунт на водной основе или Эпоксидно-цинковый грунт на водной основе 2 слоя 2×60 мкм = 120 мкм всего |
Покрытия, наносимые на месте | Толстослойный битум 150 мкм | — | — |
Номер системы | ИХ-С3-А | ИХ-С3-В | ИХ-С3-С |
---|---|---|---|
Срок службы конструкции | 50+ | 50+ | 50+ |
Срок службы покрытия | нет данных | нет данных | н/д |
Ближайший эквивалент BS EN ISO 12944-5 [3] | С3.![]() | — | С3.10 |
Подготовка поверхности по BS EN ISO 8501-1 [4] | Пескоструйная очистка до Sa 2½ | — | Пескоструйная очистка до Sa 2½ |
Заводские покрытия | Эпоксидная смола, модифицированная водородом 300 мкм | Горячее цинкование по BS EN ISO 1461 [5] (примечание 2) | i) Толстослойный эпоксидный грунт на основе фосфата цинка 80 мкм (примечание 1) ii) Толстослойный эпоксидный грунт MIO 120 мкм для повторного нанесения покрытия |
Покрытия, наносимые на месте | — | — | — |
Примечания к таблицам:
- Значения толщины, указанные для грунтовки, представляют собой общую используемую толщину и могут включать предварительную грунтовку. Например, 80 мкм может быть нанесено в один слой или в виде заводского грунта толщиной 20 мкм плюс постпроизводственного грунта толщиной 60 мкм.
- Для стальных профилей толщиной более 6 мм минимальная средняя толщина оцинкованного покрытия по BS EN ISO 1461 [5] составляет 85 мкм
- MIO — слюдистый оксид железа.
[вверх]Видимые стальные конструкции
Номер системы | IV-C2-A | IV-C2-B | IV-C2-C |
---|---|---|---|
Срок службы конструкции | 50+ | 50+ | 50+ |
Срок службы покрытия | 10 | 15 | 12 |
Ближайший эквивалент BS EN ISO 12944-5 [3] | С2.04 | С2.03 | С2.01 или С2.05 |
Подготовка поверхности по BS EN ISO 8501-1 [4] | Ручная очистка до St2 | Пескоструйная очистка до Sa 2½ | Пескоструйная очистка до Sa 2½ |
Заводские покрытия | — | Толстослойный эпоксидный грунт на основе фосфата цинка 80 мкм (примечание 1) | Акриловый грунт на водной основе или Эпоксидно-цинковый грунт на водной основе 60 мкм |
Покрытия, наносимые на месте | i) Цинк-фосфатно-алкидная грунтовка 40 мкм (примечание 2) ii) Толстослойная цинк-фосфатно-алкидная грунтовка 80 мкм iii) Алкидная отделка 60 мкм | Алкидное покрытие 60 мкм | Акрил на водной основе или Эпоксидное покрытие на водной основе 60 мкм |
Номер системы | IV-C3-A | IV-C3-B | IV-C3-C |
---|---|---|---|
Срок службы конструкции | 50+ | 45 | 40 |
Срок службы покрытия | 40+ | 25 | 20 |
Ближайший эквивалент BS EN ISO 12944-5 [3] | — | С3.![]() | С3.06 |
Подготовка поверхности по BS EN ISO 8501-1 [4] | — | Пескоструйная очистка до Sa 2½ | Пескоструйная очистка до Sa 2½ |
Заводские покрытия | Горячее цинкование по BS EN ISO 1461 [5] (примечание 3) | i) Эпоксидный грунт на основе фосфата цинка 80 мкм (примечание 1) ii) Толстослойный эпоксид MIO 100 мкм | i) Толстослойный эпоксидный грунт на основе фосфата цинка 120 мкм (примечание 1) ii) Полиуретановое покрытие с высоким содержанием твердых частиц 60 мкм |
Покрытия, наносимые на месте | (примечание 4) | Полиуретановое покрытие с возможностью повторного нанесения 60 мкм | — |
Примечания к таблицам:
- Значения толщины, указанные для грунтовки, представляют собой общую используемую толщину и могут включать предварительную грунтовку.
Например, толщина слоя 80 мкм может быть нанесена в один слой или в виде заводского грунта толщиной 20 мкм плюс послепроизводственного грунта толщиной 60 мкм.
- Для получения удовлетворительных характеристик рекомендуется грунтовка с низкой вязкостью.
- Для стальных профилей толщиной более 6 мм минимальная средняя толщина оцинкованного покрытия согласно BS EN ISO 1461 [5] составляет 85 мкм.
- Для повышения долговечности и улучшения внешнего вида горячеоцинкованное покрытие можно обработать морилкой или Т-образной пропиткой с последующим нанесением виниловой грунтовки толщиной 40 мкм и виниловым финишным покрытием толщиной 60 мкм.
- MIO — слюдистый оксид железа.
[top]Бассейны
Номер системы | СП-С4-А | СП-С4-Б | СП-С4-С |
---|---|---|---|
Срок службы конструкции | 50+ | 50+ | 50+ |
Срок службы покрытия | 10+ (примечание 1) | 25 | 25 |
Ближайший эквивалент BS EN ISO 12944-5 [3] | Г4.![]() | С4.07 | С4.11 |
Подготовка поверхности по BS EN ISO 8501-1 [4] | — | Пескоструйная очистка до Sa 2½ | Пескоструйная очистка до Sa 2½ |
Заводские покрытия | i) Горячее цинкование в соответствии с BS EN ISO 1461 [5] (примечание 2) ii) Морилка, протравливающая грунтовка или пескоструйная обработка (примечание 3) iii) Толерантная к поверхности эпоксидная смола 75 мкм | i) Эпоксидно-фосфатно-цинковая грунтовка 80 мкм ii) Пигментированная эпоксидная смола 2 слоя, всего 200 мкм | i) Эпоксидно-фосфатно-цинковая грунтовка 80 мкм ii) Эпоксидная смола MIO 2 слоя, всего 200 мкм |
Покрытия, наносимые на месте | Акрил-уретан 50 мкм | Алифатическое полиуретановое покрытие 60 мкм | Полиуретановое покрытие с возможностью повторного нанесения 60 мкм |
Примечания к таблице:
- Срок службы покрытия оценивается только для лакокрасочной системы и не включает горячеоцинкованное покрытие.
Срок службы всей системы защиты без технического обслуживания должен превышать 25 лет, однако предполагается, что из эстетических соображений техническое обслуживание будет проводиться каждые 10 лет или меньше.
- Для стальных профилей толщиной более 6 мм минимальная средняя толщина оцинкованного покрытия согласно BS EN ISO 1461 [5] составляет 85 мкм. Для скрытых металлоконструкций, напр. за подвесным потолком дополнительная обработка не требуется. Для видимых стальных конструкций поверхность оцинкованного покрытия должна быть обработана и покрыта, как показано на рисунке.
- Методы подготовки горячеоцинкованных покрытий должны обеспечивать достижение удовлетворительных условий для принятия системы лакокрасочного покрытия. Важно, чтобы стальные конструкции были тщательно обезжирены и не имели никаких загрязнений. Можно рассмотреть несколько методов, в том числе:
- Морилка или Т-образная протирка , которая представляет собой нанесение кистью химического раствора, вступающего в реакцию с оцинкованной поверхностью.
Эффективность раствора очевидна, а необработанные участки очевидны. После обработки раствор следует смыть чистой водой, а затем обработанную поверхность высушить перед покраской. Для обеспечения успешных результатов важно тщательно соблюдать инструкции производителей.
- Протравливающие грунтовки , которые могут быть одно- или двухкомпонентными материалами, и они наносятся в виде тонкопленочных покрытий толщиной от 10 мкм до 25 мкм. Версии с двумя упаковками, как правило, обеспечивают улучшенную поверхность по сравнению с одинарной упаковкой .
- Чистоструйная очистка , которая представляет собой использование мелкозернистого неметаллического абразива под низким давлением, что может быть очень эффективным, но требует осторожности и опыта. Обработка должна сделать оцинкованную поверхность слегка шероховатой без удаления покрытия.
- Морилка или Т-образная протирка , которая представляет собой нанесение кистью химического раствора, вступающего в реакцию с оцинкованной поверхностью.
- MIO — слюдистый оксид железа.
[top]Внешняя среда
Долговечность системы покрытия, указанная в следующих таблицах, основана на практическом опыте. Это ожидаемый срок службы в годах до первого капитального ремонта. Это принимается за уровень деградации Ri3 из BS EN ISO 4628-3 [6] (1% площади поверхности покрыт ржавчиной). Следует отметить, что это не подразумевает гарантии продолжительности жизни. Долговечность оцинкованных стальных конструкций определяется цифрами из стандарта BS EN ISO 14713 9.0102 [7] .
Номер системы | Е-С3-А | E-C3-B | Е-С3-С |
---|---|---|---|
Срок службы покрытия | 20+ | 20 | 20 |
Ближайший эквивалент BS EN ISO 12944-5 [3] | — | С3.07 | С3.09 |
Подготовка поверхности по BS EN ISO 8501-1 [4] | — | Пескоструйная очистка до Sa 2½ | Пескоструйная очистка до Sa 2½ |
Заводские покрытия | Горячее цинкование по BS EN ISO 1461 [5] (примечания 1 и 2) | i) Эпоксидный грунт на основе фосфата цинка 80 мкм (примечание 3) ii) Толстослойный эпоксидный грунт MIO 100 мкм | i) Толстослойный эпоксидный грунт на основе фосфата цинка 100 мкм (примечание 3) ii) Полиуретановое покрытие с высоким содержанием твердых частиц 60 мкм |
Покрытия, наносимые на месте | — | Полиуретановое покрытие с возможностью повторного нанесения 60 мкм | — |
Номер системы | Е-С4-А | E-C4-B | Е-С4-С |
---|---|---|---|
Срок службы покрытия | 15-20 | 20 | 20+ |
Ближайший эквивалент BS EN ISO 12944-5 [3] | С4.![]() | — | — |
Подготовка поверхности по BS EN ISO 8501-1 [4] | Пескоструйная очистка до Sa 2½ | Пескоструйная очистка до Sa 2½ | Пескоструйная очистка до Sa 2½ |
Заводские покрытия | i) Эпоксидная грунтовка с высоким содержанием цинка 40 мкм (примечание 6) ii) Толстослойная эпоксидная смола MIO 100 мкм | i) Эпоксидный грунт на основе фосфата цинка 80 мкм ii) Эпоксидная смола со стеклянными чешуйками толщиной 300 мкм | i) Эпоксидный грунт на основе фосфата цинка 25 мкм (примечание 7) ii) Эластомерный уретан 1000 мкм (примечание 8) |
Покрытия, наносимые на месте | Толстослойный эпоксидный материал MIO 100 мкм (примечания 4 и 5) | Полиуретановое покрытие с возможностью повторного нанесения 60 мкм | Полиуретановое покрытие с возможностью повторного нанесения 60 мкм |
Номер системы | E-C5-A | E-C5-B | Е-С5-С |
---|---|---|---|
Срок службы покрытия | 15 | 20 | 15 |
Ближайший эквивалент BS EN ISO 12944-5 [3] | ТСМ5.![]() | С5.08 | Г5.04 |
Подготовка поверхности по BS EN ISO 8501-1 [4] | Пескоструйная очистка до Sa 3 | Пескоструйная очистка до Sa 2½ | — |
Заводские покрытия | i) Напыленный алюминий в соответствии с BS EN ISO 2063 [8] [9] 150 мкм (примечание 9) ii) Цинк-фосфатно-эпоксидное защитное покрытие 50 мкм iii) Толстослойное эпоксидное покрытие MIO 100 мкм (примечание 4)33 | i) Эпоксидная грунтовка с высоким содержанием цинка 40 мкм (примечание 6) ii) Толстослойная эпоксидная смола MIO, всего 200 мкм (один или два слоя) (примечание 4) | i) Горячее цинкование по BS EN ISO 1461 [5] (примечание 1) ii) Морилка iii) Травильный грунт 40 мкм iv) Толстослойная эпоксидная смола MIO 100 мкм (примечание 4) |
Покрытия, наносимые на месте | Полиуретановое покрытие с возможностью повторного нанесения 60 мкм | Полиуретановое покрытие с высоким содержанием твердых частиц 60 мкм | Полиуретановое покрытие с возможностью повторного нанесения 60 мкм |
Примечания к таблицам:
- Для стальных профилей толщиной более 6 мм минимальная средняя толщина оцинкованного покрытия по BS EN ISO 1461 [5] — 85 мкм.
- Если по эстетическим или другим причинам требуется покраска оцинкованных стальных конструкций; можно использовать подходящие системы из BS EN ISO 12944-5 [3] .
- Значения толщины, указанные для грунтовки, представляют собой общую используемую толщину и могут включать заводскую грунтовку. Например, толщина слоя 80 мкм может быть нанесена в один слой или в виде заводского грунта толщиной 20 мкм плюс послепроизводственного грунта толщиной 60 мкм.
- MIO — слюдистый оксид железа.
- Следует отметить, что цветовая гамма MIO ограничена.
- Грунтовка с высоким содержанием цинка толщиной 80 мкм увеличивает срок службы системы примерно на 5 лет.
- Грунтовочный слой можно не наносить при условии, что базовый/промежуточный слой наносится непосредственно на чистую стальную основу с подходящим профилем поверхности.
- Со временем эластомерные уретаны могут подвергаться поверхностной деградации, известной как «меление», которая изменяет внешний вид, но не влияет на общую долговечность системы.
Там, где для улучшения внешнего вида требуется стабилизация цвета, этого можно добиться путем нанесения финишного покрытия в этой системе.
- Защита стальных конструкций от атмосферной коррозии с помощью термически напыленных алюминиевых или цинковых покрытий описана в BS EN ISO 2063-1 [8] и BS EN ISO 2063-2 [9] .
[вверх] Стены по периметру
[вверх] Стальные конструкции в четком отделении от внешней створки
Для полостей в стенах, в которых сталь остается сухой, либо за счет использования непроницаемого наружного листа, либо при физическом отделении стали от наружного листа, система из раздела «Скрытые стальные конструкции» для категорий окружающей среды C1, C2 или C3 может подойти. Обработка, указанная для полых стен, также должна подходить для внутренней среды здания. Если внутренняя среда будет более агрессивной, потребуется дополнительная защита.
Номер системы | ПВ-К2-С |
---|---|
Срок службы конструкции | 50+ |
Срок службы покрытия | н/д |
Ближайший эквивалент BS EN ISO 12944-5 [3] | С3.![]() |
Подготовка поверхности по BS EN ISO 8501-1 [4] | Пескоструйная очистка до Sa 2½ |
Заводские покрытия | Эпоксидный грунт на основе фосфата цинка (примечание 1) 80 мкм |
Покрытия, наносимые на месте | (примечание 2) |
Примечания к таблице
- Значения толщины, указанные для грунтовки, представляют собой общую используемую толщину и могут включать предварительную грунтовку. Например, 80 мкм может быть нанесено в один слой или в виде заводского грунта толщиной 20 мкм плюс постпроизводственного грунта толщиной 60 мкм.
- Окружающая среда внутри «нормальной» конструкции стены с полостью относится к категории C2. Система PW-C2-S считается подходящей для таких условий. Однако, если считается, что стальные конструкции внутри полости относятся к более агрессивной категории окружающей среды, перед или во время строительства может быть нанесено толстослойное битумное покрытие толщиной 150 мкм на поверхности стальных конструкций внутри полости.
[вверху]Стальные конструкции в контакте с внешним листом
Кирпичная кладка или другая каменная кладка со временем могут дать трещины и протечки. Когда стальные конструкции соприкасаются с наружным листом кирпичной/каменной кладки или встроены в него, следует использовать одну из следующих систем. В некоторых регионах нержавеющая сталь может потребоваться для закладных элементов в соответствии с местным законодательством или считаться необходимой для обеспечения достаточной долговечности. Следует обратиться за консультацией к специалисту.
Номер системы | PW-C2-A | PW-C2-B |
---|---|---|
Срок службы конструкции | 50+ | 50+ |
Срок службы покрытия | нет данных | н/д |
Ближайший эквивалент BS EN ISO 12944-5 [3] | — | — |
Подготовка поверхности в соответствии с BS EN ISO 8501-1 [4] | Пескоструйная очистка до Sa 2½ | — |
Заводские покрытия | Один слой эпоксидной смолы, не содержащей растворителей, 450 мкм | i) Горячее цинкование в соответствии с BS EN ISO 1461 [5] 85 мкм ii) Два слоя битума для тяжелых условий эксплуатации, всего 200 мкм |
Покрытия, наносимые на месте | — | — |
[наверх]Ссылки
- ↑ 1,0 1,1 1,2 BS EN ISO 12944-2: 2017, Краски и лаки.
Защита стальных конструкций от коррозии защитными системами окраски. Часть 2. Классификация сред, BSI
- ↑ 2.0 2.1 BS EN ISO 9223: 2012, Коррозия металлов и сплавов. Коррозионная активность атмосферы. Классификация, определение и оценка. БСИ
- ↑ 3,00 3,01 3,02 3,03 3,04 3,05 3,03 0102 3.07 3.08 3.09 3.10 3.11 BS EN ISO 12944-5: 2019, Краски и лаки, Защита стальных конструкций от коррозии системами защитной окраски, Системы защитной окраски, BSI
- ↑ 4.00 4.01 4.02 4.03 4.04 4.05 4.06 4.07 4.08 4.09 4.10 BS EN ISO 8501-1: 2007, Preparation of steel substrates before application красок и сопутствующих товаров. Визуальная оценка чистоты поверхности.
Степени ржавчины и степени подготовки стальных поверхностей без покрытия и поверхностей после полного удаления предыдущих покрытий, ISO
- ↑ 5.0 5.1 5.2 5,3 5,4 5,5 5,6 5,7 5,8 5,9 . Спецификации и методы испытаний. БСИ
- ↑ BS EN ISO 4628-3: 2016 Краски и лаки. Оценка деградации покрытий. Обозначение количества и размера дефектов, а также интенсивности однородных изменений внешнего вида. Часть 3. Оценка степени ржавчины. БСИ
- ↑ BS EN ISO 14713-1: 2017 Цинковые покрытия. Руководство и рекомендации по защите от коррозии железа и стали в конструкциях. Общие принципы конструкции и коррозионной стойкости. БСИ
- ↑ 8.0 8.1 BS EN ISO 2063-1: 2019, Термическое напыление, Цинк, алюминий и их сплавы, Вопросы проектирования и требования к качеству для систем защиты от коррозии, BSI
- ↑ 9.
0 9.1 BS EN ISO 2063-2: 2017, Термическое напыление, Цинк, алюминий и их сплавы, Выполнение систем защиты от коррозии, BSI
Ресурсы
- Хенди, Ч.Р.; Айлс, округ Колумбия (2015) Группа стальных мостов: Руководящие указания по передовой практике строительства стальных мостов (6-й выпуск). (стр. 185). SCI
- Руководство 8.01 Подготовка к эффективной защите от коррозии
- Руководство 8.03 Горячее цинкование погружением
- Руководство 8.04 Металлические покрытия, полученные термическим напылением
- Руководство 8.05 Высокоэффективные лакокрасочные покрытия
- Стальные здания, 2003 г., Британская ассоциация строительных металлоконструкций, ООО.
- Глава 12 – Защита от коррозии
[наверх]Дополнительная литература
- D.Deacon & R.Hudson (2012), Steel Designer’s Manual (7th Edition), Chapter 36 – Corrosion and anticorrosion Prevention, The Steel Construction институт.