Сварка днища авто: советы и обзор оборудования
Днище автомобиля быстрее подвергается воздействию воды, грязи и дорожных реагентов, чем остальная часть кузова. А если наехать на высокий бордюр или гребень асфальта, то деформации ускоряют порчу металла еще больше. Кстати, из личного печального опыта отмечу, что на такие препятствия лучше заезжать колесом, а не брать их промеж колес, если клиренс менее 160 мм. Итак, расскажу, как выполнить ремонт днища автомобиля сваркой, какие аппараты считаю лучшими для этого и поделюсь специфическими нюансами процесса сварки.
Способы сварки, оборудование и материалы
Сварка днища автомобиля невозможна без сварочного оборудования, поэтому сразу начну с описания наиболее подходящих для этого аппаратов и расходных материалов. Разделю их по методам сварки.
Полуавтоматическая сварка днища авто
Считаю этот метод самым лучшим, поскольку работа дается легче и выполняется быстрее. Для сварки днища машины полуавтоматом рекомендую такие модели:.
- ПТК МАСТЕР MIG 180 F15 — простой и надежный бюджетный полуавтомат для гаража. Если хотите варить машину сами — отличный выбор.
- Сварог REAL MIG 200 (N24002N) — тоже простой аппарат, но уже на 200 А (может пригодиться для сварки более толстого металла, например ворот, петель калитки).
- AuroraPRO OVERMAN 200 — еще один бюджетник для ремонта сваркой днища, но он способен работать при просадках входящего напряжения до 140 В. Актуально, если в вашем гараже такие проблемы с электричеством.
- Fubag INMIG 200 SYN Plus — полупрофессиональная машина, в сторону которой нужно смотреть уже мастерам автосервисов и народным умельцам. Тонкие настройки обеспечат комфорт при работе с металлом днища.
- KEMPPI MinarcMIG EVO 170 — надежный и долговечный полуавтомат с графическим дисплеем. При силе тока 100 А можно варить беспрерывно, что важно для продолжительной работы в автосервисе/СТО.
- ТЕРМИТ ВДИ-200 — маленький и легкий аппарат 3.
- Ресанта САИ 220 — бюджетный инвертор с простыми настройками. Устойчив к колебаниям в сети.
- Сварог REAL ARC 200 (Z238N) — аппарат с улучшенной защитой корпуса для гаражных условий. Отличается стабильным горением дуги и наличием функции Antistick.
- Ресанта САИ 250ПН — инвертор РДС варит при входном напряжении 140 В.
- ТОР Торус-210 Комфорт — аппарат российской сборки с тремя вспомогательными функциями: Arc Force, Antistick, Hot Start.
- com/embed/WFqz-kJXfxE» title=»YouTube video player» frameborder=»0″ allow=»accelerometer; autoplay; clipboard-write; encrypted-media; gyroscope; picture-in-picture» allowfullscreen=»»/>
Рекомендую, чтобы сварочная проволока для ремонта днища авто была омедненная. Тогда шов будет лучше сопротивляться постоянным вибрациям, присутствующим на кузове. Купите, например, проволоку ESAB OK Autrod 12.51 диаметром 0.8 мм.
Ручная дуговая сварка днища авто
Сварка днища автомобиля электродом и инвертором происходит медленнее, чем полуавтоматом, и сам сварщик должен обладать уже определенными навыками для контроля дуги (полуавтоматом новичкам работается легче). Для профессиональной деятельности такой метод не рекомендую ввиду низкой скорости, а вот для сварки днища автомобиля своими руками вполне подойдет. Цена инверторов РДС гораздо доступнее полуавтоматов. Если подумываете о покупке сварочного аппарата, советую взглянуть на:
Советую купить электроды ESAB OK 46.00 диаметром 2-3 мм. Они подходят для сварки во всех пространственных положениях и неприхотливы к чистоте металлической поверхности.
Обзоры и практика применения оборудования,
инсайды производителей, новости!
Читайте бесплатно эксклюзивные материалы нашего блога.
Знания в 2021 году самый ценный из ресурсов!
Подготовка днища перед сваркой
А теперь поговорим непосредственно о самом процессе ремонта днища сваркой. Сперва поверхность нужно подготовить. В идеале днище лучше обработать пескоструем, чтобы увидеть полную картину состояния металла и легче возбуждать дугу. Если пескоструя нет, пройдитесь щеткой по металлу, убрав ржавчину.
Простучите молотком поверхность, ища звонкие, резонансные места — там железо самое тонкое.
Откровенные дыры следует повырезать болгаркой до цельного металла, иначе материал продолжить гнить даже внутри конструкции. В труднодоступных местах используйте ножницы по металлу. Приготовьте нарезанные сегменты, соответствующие форме закрываемых участков (латки). Толщина металла допустима 1-2 мм.
Нюансы сварки днища автомобиля
Банальные вещи про отключение клеммы АКБ и пр. описывать не буду — расскажу о неочевидном. Сперва извечный вопрос, который должен породить много комментариев под темой: варить днище встык или внахлест? Есть «за» и «против» у каждого способа. Латка строго по контуру дыры в днище выглядит аккуратно, но придется наложить сплошной шов. Есть большой риск деформации и просадки металла. Он перегреется, что ухудшит его прочностные характеристики и сопротивляемость коррозии. При методе встык долго придется подгонять размер заплаток, чтобы избежать широких зазоров.
Латки внахлест выглядят менее привлекательно, но это под машиной, поэтому кто их там видит?! Зато сварка внахлест:
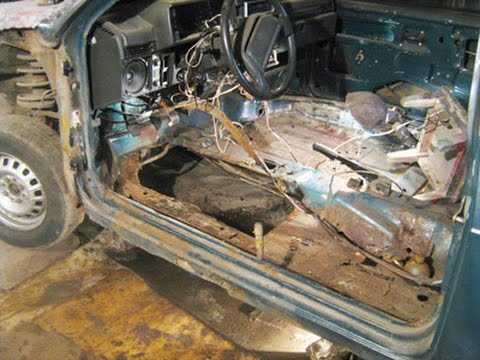
Мое мнение — варить внахлест. Прикладываете металл и выполняете прихватки. Затем проваривает короткими швами по 15-20 мм с таким же интервалом. Дугу зажигайте на новом металле и переносите на стык — так будет меньше прожогов. Чтобы не было «гармошки», варите соединение не слева-направо, а начинайте с конца стыка, но каждый шов ведите слева-направо. Еще больше тонкостей по сварке кузовного металла посмотрите в нашей статье.
Чем обработать днище снаружи после сварки
Если днище не покрыть защитным слоем, то оно сгниет за следующие пару лет. Подтверждением служит срок службы банки глушителя — она не обработана и ее хватает максимум на 3 года. А у нас еще и шов прерывистый, куда будет попадать влага. Предлагаю такой порядок действий и чем обработать днище автомобиля после сварки снаружи:
- Покрываете металл грунтовкой для кузова.
- Даете ей высохнуть.
- Обрабатываете битумными составами «Антикор битумный», «Автоантикор эпоксидный», «Мастика битумная».
Это эластичные средства, хорошо удерживающиеся на вибрирующей поверхности. Уделите особое внимание местам стыковки, чтобы заполнить щели. Внутри салона рекомендую, если имеется доступ к стыку, пройтись герметиком или задуть воском.
Популярные вопросы и ответы по теме:
- В каком положении лучше всего варить днище автомобиля?
- Какую толщину листа заплаток выбрать?
- Как согнуть прикладываемое железо по форме днища без газосварки?
- Как избежать прожогов металла?
- Как заварить дыру?
На эстакаде или подъемнике придется варить в потолочном положении. Это подходит только для установки небольших заплаток. Объемные сварочные работы по днищу авто рекомендую проводить, завалив машину на бок. Снимаете колеса с одной стороны и подкладываете их под стойки кузова на другой стороне. Чтобы поднять авто, понадобится 5-6 человек. Упираться в стойки нужно резиной, а не диском. Снизу можно подстраховаться и подставить толстый брус.
Если вы начинающий сварщик, железо на днище тонковатое, ремонт ведется на прямом участке, возьмите 1. 5-2 мм. В случае «набитой руки» и «живого» металла на днище, используйте 1.0 мм — легче будет гнуть.
Рельефные участки на днище лучше всего подгибать, используя подогрев автогеном. Если его нет, провариваете шов 15 мм непосредственно перед местом сгиба и, пока металл горячий, молотком подбиваете его до следующего места прихватки. Так постепенно подгибаете латку по всему периметру, используя нагрев от наложенного шва. Затем перед обваркой можно простучать молотком еще, чтобы уменьшить зазоры.
Держите дугу на толстом металле (латке), кратковременно перенося ее на тонкий. Это прогреет стык, но старое железо не прожжется. Более подробные приемы я приводил в схожей статье про сварку порогов.
При сварке днища электродом неизбежны прожоги, особенно когда пытаются выполнить локальный ремонт, чтобы не менять днище полностью. Прожженное отверстие заваривают по кругу, прерывистой дугой, давая остывать наплавленному металлу. Так наращиваются стенки и отверстие постепенно сужается до полного заваривания.
Если после прочтения статьи у Вас все равно остались вопросы — обязательно задавайте их в комментариях! Я с удоволствием на них отвечу или же опишу в отдельной статье.
Сергей Шевцов
Сварщик и специалист демо-зала
Сварка днища автомобиля своими руками
Автор Сварщик На чтение 5 мин Опубликовано
Для машины с большим пробегом, коррозия днища – вещь обычная. Механические повреждения, повышенная влажность, антигололедные реагенты со временем разрушают железо. Металл превращается в труху. Ездить на таком авто опасно, машине нужен ремонт. Обращаться в СТО не выгодно, мастера могут насчитать лишнего. Имея сварочный аппарат, несложно произвести сварку днища автомобиля в гараже. Важно учесть некоторые нюансы, придерживаться технологии. Работы удобнее проводить вдвоем, напарник поможет зафиксировать латку перед прихватом.
Содержание
- Инструменты и материалы
- Подготовительные работы
- Процесс сварки
- Чем обработать днище после сварки
- Полезные советы
Инструменты и материалы
Чтобы заварить днище, помимо сварочного оборудования потребуются расходные материалы. Выбирая, каким варить металлом, необходимо учитывать два момента:
- тонкую сталь труднее приваривать, нужен опыт, чтобы выбрать температурный режим, исключающий риск прожогов;
- толстое железо сложнее обрабатывать.
Заплатки делают из металла толщиной от 1 до 2 мм – это оптимальные параметры.
Что понадобится при работе:
- сварочный аппарат, при работе ручной дуговой сваркой понадобятся тонкие электроды, максимальный размер 1,6 мм; для полуавтомата нужна медная проволока и углекислота;
- болгарка с режущими и шлифовальными насадками;
- газосварка плюс карбид, кислород для очистки от ржавчины в труднодоступных местах;
- обычные или электроножницы по металлу, ими вырезают латки;
- электродрель;
- молоток, им простукивают днище авто для выявления дефектов;
- зубило или перфоратор, чтобы снять шумоизоляцию;
- отвертка или шуруповерт.
Днище просматривают на эстакаде или в смотровой яме при хорошем освещении. Металл простукивают молотком, проверяя на прочность. Понадобится подъемник, чтобы обеспечить доступ к поврежденным участкам.
Потребуется преобразователь ржавчины, шумоизоляционные покрытия; антикоррозийные составы; грунтовку по металлу; растворитель или другой обезжиривающий состав.
Непредвиденные расходы
Необходимо предусмотреть покупку запчастей. Их нужность определяют после осмотра автомобиля. При ремонтных работах меняют ветхие элементы машины:
- прогнившие и гнутые пороги, их снимают в первую очередь, при установке контролируют геометрию кузова;
- лонжероны пола;
- напольные панели, они монтируются снизу;
- тормозные и топливные трубки, прикипевшие к металлу.
Иногда требуют замены и другие элементы машины. Впрок запчасти лучше не приобретать, они могут не понадобиться.
Подготовительные работы
Когда железо прогнило в нескольких местах, проще переварить днище целиком. В ряде случаев замена выгодней установки большого числа металлических заплат. Ремонт днища автомобиля своими руками начинается с подготовительного этапа. Участки с крупными дефектами вырезают, мелкие — достаточно очистить от ржавчины. Когда сложно добраться шлифовальным кругом, закрепленным на болгарке, включают газосварку.
Зоны швов на машине и латках покрывают преобразователем ржавчины, затем зачищают до блеска. После этого обезжиривают. Латки подгоняются под конфигурацию днища с помощью нагрева, металл легче деформируется, или специальных гнущих устройств.
Процесс сварки
Перед огневыми работами, в целях безопасности, обязательно демонтируют бензобак. Латку сначала прихватывают в 3–4 точках, затем полностью обваривают. Мелкие дефекты заправляют короткими швами до 3 см длиной. Сваркой днища в одиночку заниматься сложно. Когда напарник придерживает заплату, ремонт ускоряется.
Важно, чтобы латка плотно прилегала к месту ремонта. Зазоры повышают риск коррозионных разрушений. Швы для прочности проковываются молотком. При хорошем освещении все участки ремонта проверяют. При необходимости проваривают соединение снова. Только после осмотра приступают к зачистке шовных валиков.
Чем обработать днище после сварки
Перед нанесением защиты от коррозии сначала используют грунтующие составы. Их наносят на чистые поверхности по инструкции, просушивают. Грунтовка обеспечивает надежное сцепление стали с антикором. Производители предлагают различные составы:
- Tectyl выпускают в трех модификациях: а) классический создает органическую микропленку; б) Tectyl цинк обеспечивает дополнительное цинковое покрытие, защищающее металл от действия солей; в) Tectyl НТ цинк предназначен для интенсивной эксплуатации в условиях городской среды;
- Мовиль – экономичное средство, зарекомендовавшее себя на протяжении полувека;
- битумная мастика выпускается на каучуковой, полимерной, минерально-сланцевой и полимерной основе;
- Dinitrol на основе полимерной резины.
После сварки кузовных деталей машины обязательно восстанавливают шумоизоляцию. Для покрытия днища удобен Prim антишум с резиновой микрокрошкой. Состав разводится водой, одновременно выполняет роль шумовой изоляции и антикора.
Перед нанесением защиты от коррозии сначала используют грунтующие составыПолезные советы
Для ремонта днища автомобиля своими руками специалисты рекомендуют использовать полуавтоматы. Присадка подается с фиксированной скоростью, горелка обеспечивает равномерный нагрев. Шов получается качественным, ровным. При работе с электродами удобен инвертор с дополнительными функциями, поддерживающими постоянный режим работы. Они снижают риск залипания электрода.
До раскроя листа металла определяют точные размеры зоны дефектов. Заплатка должна подходить по размеру, прилегать по геометрии. Для деформации лист долго не прогревают – снижаются прочностные характеристики сплавов, они становятся рыхлыми. Движения руки с держателем или насадкой должны быть равномерными, без рывков. Большие участки соединяют прерывным швом, промежутки оставляют до 3 см. Такие соединения лучше выносят динамические нагрузки, повышаются прочностные параметры кузова. Подобные соединения требуют прочного изоляционного покрытия. Мастика спасает от попадания влаги в микроскопические зазоры.
Для работы с оцинкованным железом применяют защитные флюсы, они сохраняют покрытие от вскипания и выгорания. Зная тонкости процесса, выполнить соединение несложно. Главное – не торопиться, тщательно подготовить поверхности перед работой. Нельзя пренебрегать антикоррозийными работами. Днище подвергается большой химической нагрузке в процессе эксплуатации. Защитные составы наносят ровным слоем.
Body Shop Welding
Вы когда-нибудь слышали историю об инструкторе по сварке, который говорит своему классу: «Поднимите руку, если вы считаете себя отличным сварщиком». Все 10 учеников поднимают руки. Затем он заставляет их выполнить практическую сварку, а затем разрушает сварные швы. Увидев результаты, инструктор снова предлагает классу поднять руки. На этот раз поднимаются только две руки.
Вы можете думать, что ваши техники хорошие сварщики, но так ли это? Откуда вы знаете? С недавним COVID-19кризиса, смогли ли вы сохранить всех своих техников? Вы работаете с новыми техниками? Вам нужно повторно нанять новый персонал? Как вы определяете техника, который был должным образом обучен? Взгляните на ваших нынешних сотрудников, проводите ли вы их регулярное обучение? Проводятся ли разрушающие испытания сварных швов на аналогичных деталях перед каждым сварным швом? Регулярно ли проводится техническое обслуживание ваших сварочных аппаратов? Просматривают ли ваши технические специалисты информацию и рекомендации по ремонту оригинального оборудования? Иначе как бы они узнали, из каких материалов изготовлен автомобиль и какой метод сварки рекомендуется? Готовы ли вы взять на себя ответственность за неудачный сварной шов? Или несоблюдение рекомендованных автопроизводителем процедур ремонта? Чтобы понять, насколько важно следовать рекомендациям по оригинальному оборудованию, достаточно заглянуть в иск Джона Игла.
Нагрев
Автопроизводителям все чаще требуются методы сварки, минимизирующие нагрев и уменьшающие зону теплового воздействия (ЗТВ). Это тема сегодня, так как все больше и больше автомобилей используют металлы, а слишком высокая температура может негативно повлиять на их структурную целостность. Эти металлы включают высокопрочную сталь (HSS), сверхвысокопрочную сталь (UHSS), сплавы бора и многое другое.
Перед каждым сварным швом в вашем цеху должны проводиться разрушающие испытания сварных швов. ЗТВ на UHSS ослабляет свои свойства и может создавать слабые места или даже зоны разрушения в местах, где их быть не должно. Во многих новых применениях инженерной стали большая часть прочности и свойств может быть разрушена при довольно низких температурах, что ставит под угрозу целостность автомобиля. Неправильное использование тепла или несоблюдение техническими специалистами процедур защиты от коррозии во время сварки, после сварки или использования любого источника тепла подорвет целостность автомобиля — если не из-за самого тепла, то со временем из-за проблем с коррозией. Усердие в наблюдении или размещении процедур контроля качества в магазине — это не просто мысль, а требование. Там, где OEM может разрешить нагрев, технические специалисты должны контролировать, сколько и как долго можно использовать тепло. Единственный процесс, которому необходимо следовать, — это соблюдение всех рекомендаций оригинального оборудования.
Давайте рассмотрим некоторые методы сварки, которые все больше и больше рекомендуются OEM-производителями.
Пайка MIG
Пайка MIG удовлетворяет потребность в прочном соединении при меньшем нагреве. Сварка стали MIG/MAG использует тепло для расплавления основных металлов и сплавления их с присадочной проволокой. Это плавление создает большую ЗТВ, в которой многие металлы подвергаются риску. В зависимости от свариваемого металла, стали плавятся при температуре около 3000 градусов по Фаренгейту или 1650 градусов по Цельсию. Эти температуры необходимы для плавления металлов. Добавьте к этому использование маломощных 110-вольтовых сварочных аппаратов, и излучаемое тепло создает большую тепловую сигнатуру там, где ЗТВ выходит за пределы зоны сварки. Несмотря на то, что сварной шов прочный, тепловые и коррозионные повреждения возникают дальше. Это изменение свойств стали вдали от сварного шва становится большой проблемой для UHSS, поскольку может образоваться зона разрушения там, где ее быть не должно. Кроме того, ухудшаются коррозионные свойства.
Пайка MIG имеет гораздо более низкую температурную сигнатуру, или HAZ, из-за разницы в тепле, используемом во время пайки. Сварка сталей MIG/MAG представляет собой процесс плавления металлов. Пайка MIG представляет собой адгезионный процесс, в котором используется тепло до 1940 градусов по Фаренгейту. При пайке не расплавляются основные металлы, только присадочная проволока. Присадочная проволока течет при низком нагреве и оседает на поверхность или между металлами. Эта площадь поверхности, или след, довольно велика по сравнению со сварным швом и придает процессу пайки прочность для работы. Присадочная проволока из медно-кремниевой бронзы растекается при нагревании и обладает невероятной способностью к поверхностному натяжению после охлаждения.
Этот низкотемпературный процесс ограничивает повреждение сталей HSS и UHSS. Пайка MIG позволяет склеивать HSS и UHSS там, где контактная сварка методом продавливания (STRSW) невозможна. Читая требования некоторых производителей к пайке MIG, вы увидите заявление: «Используйте пайку MIG там, где STRSW недоступен». Сварка электрозаклепками MIG/MAG невозможна. В этих заявлениях подчеркивается необходимость обучения и обучения процессам соединения транспортных средств с использованием сварки и/или необходимых клеев.
Пайка MIG оказывает меньшее влияние на оцинкованную сталь, позволяя стали сохранять большую часть своих свойств защиты от коррозии. Уже одно это является значительным улучшением долговечности ремонта. Добавьте технику пайки, и негативное воздействие тепла еще больше уменьшится по сравнению со сваркой. Обучение тому, как работает MIG-пайка и как использовать методы, является обязательным для всех техников. Процедуры защиты от коррозии всех сварных и паяных соединений также имеют решающее значение для технических специалистов.
Точечная сварка
Точечная сварка (или STRSW) представляет собой тип сварки сопротивлением, используемый для сварки различных изделий из листового металла посредством процесса, в котором точки соприкосновения металлических поверхностей соединяются под действием тепла, полученного в результате сопротивления электрическому току.
Аппарат для контактной точечной сварки прижимного типа создает точечные сварные швы, очень быстро выделяя тепло, одновременно прикладывая давление к сварному шву. Это делается невероятно быстро, чтобы не создавать тепло, которое расширится и негативно повлияет на механические свойства окружающей стали. Если окружающая сталь повреждена, то функциональность и прочность сварного шва ослабевают. Это также может вызвать проблемы с коррозией или появление горячих точек. Эти проблемы обычно связаны со сваркой электродами MIG/MAG, поскольку STRSW создает сварные швы так быстро, что эти проблемы, как правило, уменьшаются.
Сварка
Мы видели STRSW в течение многих лет. Большинство автопроизводителей предпочитает эту сварку по многим причинам. Теперь добавьте в смесь клей. Когда мы объединяем два процесса, преимущества значительно возрастают. Сварка STRSW через клеи, которые сначала наносятся между панелями, дает некоторые замечательные преимущества. Магазины, не использующие эту процедуру там, где это требуется в процедурах ремонта, упускают из виду общую картину и, возможно, подвергают себя гарантийным обязательствам, а также ситуации с ответственностью.
Оборудование STRSW
Вы слышали, что современные автомобили не принадлежат вашему отцу. Нынешние сварщики тоже не папины. Многие из них более технологичны, «умны» и проще в использовании.
Многие могут не только автоматически определять толщину панели и тип металла, но также автоматически устанавливать требуемую мощность сварки, время сварки и давление на конце. Если в вашем цеху сваркой занимается несколько человек, они могут сохранить свои индивидуальные настройки в сварочном аппарате и получить их нажатием кнопки, когда снова будут готовы к сварке. В одной компании есть сварщик, который может обучать техников прямо на самой машине с помощью обучающего видео на ЖК-экране. Многие с мультифункциями на каждой машине. Сварщик больше не занимается только сваркой стали. Времена громоздких, тяжелых головок, которые техники с трудом используют и получают доступ к труднодоступным областям, меняются. Если в вашем магазине еще нет одного из этих сварочных аппаратов, вы отстаете и, возможно, не можете выполнять сварку, которую требует OEM.
Для тех, кто не видит смысла тратить большие деньги на более способных сварщиков, имейте в виду, что лучше не только качество сварки; отношение и моральный дух в магазине также улучшаются, что бесценно.
Это лишь краткий обзор того, что нужно и требуется для автомобилей вчерашнего, сегодняшнего и завтрашнего дня. Каждый определенный процесс потребует часов для детализации и обучения. Ищите местных поставщиков и получайте информацию, а также обучение. Использование компании для внедрения контроля качества в вашем магазине также может быть бесценным и поучительным.
Разрушающие испытания сварных швов — BodyShop Business
Более 15 лет я был экспертом по качеству сварных швов в компании I-CAR в штате Вашингтон. Все эти 15 лет сваривалась сталь, но затем I-CAR ввел тест качества сварки алюминия. Я руководил программой подготовки, испытаниями и проверкой сварных швов — в то время это был двухдневный процесс.
За это время я просмотрел и проверил тысячи сварных швов, выполненных техниками во время испытаний. Первоначальный тест качества стальных сварных швов и процесс проверки были разработаны с помощью I-CAR Американским обществом сварщиков (AWS). Это был первый практический тест, разработанный для индустрии ремонта после аварии, и его цель состояла в том, чтобы проверить способность техника по ремонту после аварии правильно и безопасно сваривать поврежденный при аварии автомобиль в соответствии с процедурами, рекомендованными производителем. Это важно, потому что с появлением автомобиля с цельным кузовом факторы энергии столкновения были тщательно спроектированы в автомобиле, чтобы обеспечить максимально безопасную деформацию конструкции автомобиля и обеспечить максимальную защиту пассажиров.
Когда компания General Motors произвела Z06 Corvette с алюминиевой рамой, она требовала, чтобы любой дилер, желающий продать Z06 Corvette, должен был, по крайней мере, одному сотруднику пройти проверку качества алюминиевой сварки I-CAR — доказательство того, что OE и страховщики также осознавали, насколько критично качество сварки для надлежащего и безопасного ремонта автомобиля, поврежденного в результате столкновения.
Стальные цельнолитые автомобили по-прежнему используют более прочные стали. Дешевый бензин иссяк, как и жажда больших и тяжелых внедорожников. Чем легче автомобиль, тем он экономичнее. Более легкие автомобили означают более легкую сталь, а это означает, что прочность стали должна увеличиваться, а толщина должна уменьшаться. Но в этом сценарии есть проблема: чем прочнее становятся эти передовые высокопрочные стали, тем более они чувствительны к нагреву. Некоторые сварные швы могут снизить свою прочность на целых 50 процентов.
В связи с тем, что эти передовые материалы используются в конструкции транспортных средств для уменьшения прибавки в весе и сохранения методов конструирования автомобилей с цельным кузовом и с пространственной рамой, становится жизненно важным использовать надлежащие методы сборки при столкновении для безопасного ремонта автомобилей, поврежденных в результате столкновения.
Причина для беспокойства
За 15 лет проверки тысяч сварных швов я получил лишь около 38% положительных результатов! Это означает, что 62 процента учащихся не прошли тест и должны были сдать его снова.
В наших тестовых центрах не было занятий по подготовке к тесту на сталь, но всем учащимся были предоставлены учебные материалы, в том числе видеоролики, в которых объяснялось, как подготовиться к тесту.
Администратор теста часто спрашивал студентов, практиковались ли они. Обычный ответ был: «Мне не нужно практиковаться, я делаю это каждый день». Проблема в том, что они делают это на машинах клиентов! Если они терпят неудачу на хорошем, чистом металле в оптимальных условиях, меня пугает мысль, что, черт возьми, происходит с автомобилями, над которыми они работают каждый день.
Внешний вид обманчив
Когда 18 лет назад компания I-CAR впервые выпустила тест качества стальных сварных швов, я подписался на него. Я заплатил за свой хлеб, и мне прислали подготовительные материалы, учебное пособие и видео. Я изучил подготовительные материалы и приготовился к работе в соответствии с рекомендациями, чтобы попрактиковаться и провести деструктивные испытания учебных сварных швов. Они выполняются так же, как сварные швы, которые вы будете выполнять во время фактического испытания. Учебный материал четко описывает весь процесс.
Я выполнил хорошо выглядящие сварные швы в угловом, пробковом и стыковом шве с подкладкой (последующие испытания были расширены за счет включения открытого стыкового шва без подложки и дополнительного испытания сварного шва, включая фактические процедуры разрезания) как в вертикальном положении (не горизонтальный) и потолочное положение – всего шесть сварных швов на тот момент.
Я визуально проверил свои сварные швы с помощью прилагаемого контрольного калибра (Фото 1) . Все выглядело нормально… никаких зазоров, отверстий не было заделано, никаких прожогов и все сварные швы были правильно измерены прибором.
Затем я начал разрушающее испытание сварных швов, следуя прилагаемым инструкциям. Угловой шов, тонкий… правильный отрыв в потолочном и вертикальном положении. Сварные швы… э-э, провал в вертикальном положении, недостаточно отрыва. Этот сварной шов мне тоже показался прекрасным! Штепсельная вилка была в порядке; Я получил больше проникновения в положении над головой, чем в вертикальном.
Затем я провел разрушающее испытание стыкового сварного шва с подложкой. Для этого требуется усилие с помощью тисков, зубила и тяжелого молотка. Вертикальный шов снова не получился. Дэн! Я никогда бы не догадался. Это выглядело хорошо, и это моя точка зрения: внешность обманчива!
Самые плохие и самые опасные сварные швы — это те, которые хорошо выглядят или даже красивы, но не имеют провара и обречены на провал. Красивый сварной шов не является признаком крепкого сварного шва.
О, прямо сейчас я слышу «болтливых набобов негативизма», и они говорят что-то вроде: «Я наложу свои сварные швы против любого». Ладно, ладно, так можно наложить красивый сварной шов. Я соглашусь с этим, но пока это не будет подвергнуто разрушительным испытаниям, вы не знаете наверняка, выдержит оно или нет. Проверять его нужно деструктивно непосредственно перед тем, как сделать такой же сварной шов на автомобиле заказчика. Поверьте, это имеет решающее значение.
Следование инструкциям
Многие из тех тысяч сварных швов, которые я тестировал, выглядели просто отлично. Они прошли визуальные параметры теста: правильной длины, не слишком короткие и не слишком длинные. Почему это важно, спросите вы? Потому что это говорит о способности техника читать, понимать и следовать инструкциям.
Угловой шов и стыковые швы имеют требования к длине. Если вы не соответствуете предписанным требованиям теста, вы провалите визуальный тест. У вас могут быть самые прочные и красивые сварные швы, но если они не соответствуют требованиям по длине, вы просто провалили испытание. Поэтому нужна практика.
Позвольте мне задать вам вопрос: если требования требуют сварного шва с проплавлением от 1 до 1,5 дюймов, зачем кому-либо производить сварной шов длиной 15/16 или, возможно, 1-9/16 дюймов? ? Эти длины не являются требуемыми длинами теста качества сварки I-CAR. Я видел сотни тестов, которые попали в эту категорию провальных.
Мастера по ремонту автомобилей привыкли делать все по-своему, в большей степени, чем механики, которые привыкли следовать точным инструкциям в рекомендуемой последовательности сборки с точным моментом затяжки. Таким образом, выполнение процедуры точным способом несколько не характерно для многих специалистов по столкновению… не для всех, но, по моим наблюдениям, около 62 процентов. Странно было то, что во втором тесте проходной балл вырос с 38 процентов до 9.0 процентов. Это подсказало мне, что если кому-то придется заплатить дополнительные деньги, чтобы сдать второй тест, то этот кто-то не будет очень доволен.
Страх как мотиватор
Таким образом, при правильном вдохновении подавляющее большинство техников могут пройти тест. Я видел, как эта политика разыгрывалась и по-другому. Когда технические специалисты в конкретном цеху одновременно проходили тест на качество сварки, либо все они имели 38-процентный проходной балл, либо все сдавали экзамен! Я предполагаю, что, когда владелец магазина или менеджер понимал, сколько денег стоит пройти тест, они проявляли личную заинтересованность в том, чтобы увидеть, как идет практика, и просили визуальные результаты прохождения сварных швов задолго до того, как кто-либо действительно проходил тест. Я знаю, что делал то же самое, лично работая со своими техниками, чтобы убедиться, что они понимают, как практиковать и деструктивно проверять эти учебные сварные швы.
Я знал большинство владельцев и менеджеров тех магазинов, чьи техники имели высокие проходные баллы. Это те, кто активно взаимодействует со своим народом. Они также полностью понимают вопросы ответственности, связанные с тем, что мы делаем, и делают все возможное, чтобы произвести безопасный, качественный ремонт без ответственности и защитить инвестиции и благополучие своих клиентов. Они профессионалы.
Где я могу проверить?
Возможно, тест качества сварки I-CAR недоступен для вас. Однако это может быть, учитывая, что он мобильный и может прийти к вам, если он находится в вашем районе.
Но что делать, если вы вне зоны досягаемости? Вы должны, по крайней мере, настроить и проверить себя и своих специалистов, чтобы убедиться, что вы производите высококачественные, безопасные и прочные сварные швы, прежде чем выполнять больше сварки конструкций. Рельсы рамы, основные опоры, панели днища, пороги, стойки A, B, C и D, поперечины и пороги требуют контрольной сварки перед фактической сваркой на автомобиле клиента.
Я не могу показать вам точные требования теста качества сварки I-CAR, потому что это было бы похоже на мошенничество, но я покажу вам, как правильно проверять ваши сварные швы и как выглядит проходной балл. Вы поставляете практику сварки и физические усилия.
Купоны
Для целей данного обсуждения мы будем использовать три основных и распространенных сварных шва, используемых в цеху: угловой шов, сварной шов пробкой и стыковой шов с подкладкой.
Начнем с металла, который будем сваривать. Он должен быть похож на конструкционную сталь, используемую в автомобилях с цельным кузовом. Обычно это калибр 18 с легким цинковым покрытием (гальванель или оцинковка). Вы можете пойти к поставщику стали и купить ее, или вы можете вырезать сталь из металлолома, который вы сохранили от автомобилей, над которыми вы работали. Вы должны отрезать несколько частей от поврежденной детали, которую вы заменяете, и выполнить серию сварных швов, которые вы все равно будете использовать при установке новой структурной детали. Мы назовем эти части «купоны».
Я собрал купоны на фотографиях в этой статье из сварных швов, выполненных в рамках теста качества сварки I-CAR. Они были сварены студентами, а затем подвергнуты разрушающему испытанию мной и сохранены для практических целей. Они размером 3 дюйма на 5 дюймов и имеют легкое гальваническое покрытие, имитирующее конструкционную сталь, используемую в автомобилях. Вы должны сделать их все такого размера, потому что это удобный тестовый размер для работы.
Вам также понадобится пара кусков уголка, чтобы сделать зажимное приспособление, к которому можно прикрепить купоны при сварке. Я использовал куски размером 1,5 на 1,5 на 1/8 дюйма и зажал их в тисках, чтобы можно было использовать зажимы для тисков и зажать купоны под углом, удерживаемым тисками (Фото 2) .
Очистите купоны
Очистите купоны от краски, грунтовки или других загрязнителей сварного шва. Делайте это хорошо, потому что от этого зависит качество сварного шва. Пористость в сварном шве (воздушные карманы) вызвана, среди прочего, грязным местом сварки. Избавьтесь от догадок. Если это предсказуемо, то это можно предотвратить. Ваша цель — получить хороший сварной шов с первого раза, а не просмотреть два десятка купонов, как будто вы пытаетесь создать фотодемонстрацию всех возможных дефектов сварки.
Когда купоны очистятся от загрязнений на поверхности, протрите средством для удаления воска и жира и высушите чистым полотенцем (Фото 3) .
Угловой сварной шов
Этот сварной шов не требует дополнительной подготовки, поскольку все, что вам нужно сделать, это соединить вместе два образца, при этом верхний образец должен перекрывать нижний образец посередине (Фото 4) .
Длина сварного шва должна составлять от 1 до 1-1/2 дюйма с полным отрывом между этими длинами. Другими словами, минимум 1 дюйм и максимум 1-1/2 дюйма; все, что ниже или выше этого, следует считать неудачей. Давай, говоришь? Эй, это целый ½-дюймовый стадион, на котором вы должны играть!
Отметьте расстояние в 1-¼ дюйма и используйте черный маркер, чтобы его было видно. Начните и остановитесь там, где есть черные метки. Настройте свой сварочный аппарат, как в реальной жизни, и выполните сварку (Фото 5) .
Разрушение сварного шва
Зажмите нижний образец в тисках так, чтобы сварной шов и верхний образец находились непосредственно над губками тисков. Зажмите плоские клещевые тиски на верхнем образце и отломите образец от сварного шва (Фото 6) . Осмотрите верхний купон на наличие признаков разрыва сварного шва. Сварной шов должен оставаться на нижнем образце, а верхний образец должен иметь разрыв минимум 1 дюйм и максимум 1-1/2 дюйма (Фото 7) . Этот сварной шов соответствует требованиям, но если ваш не соответствует требованиям, отрегулируйте машину соответствующим образом.
Накладной
Установите свой купон так же и отметьте его, как и при вертикальном шве, только теперь вы собираетесь сваривать накладной, как иногда приходится делать под автомобилем (Фото 8) .
Проведите разрушающий контроль этого сварного шва так же, как и вертикальный угловой шов. Если сварка не удалась, отрегулируйте машину и технику, пока не завершите проходной шов. Задокументируйте настройки вашего аппарата, чтобы при выполнении сварки в этом положении на автомобиле, над которым вы работаете, вы могли настроить сварочный аппарат соответствующим образом.
Пробковый сварной шов
Для этого сварного шва потребуется отверстие диаметром 8 мм или 5/16 дюйма, пробитое в верхнем купоне. Вварите это отверстие в верхнем купоне в нижний купон, а затем открутите верхний купон, оставив сварной шов в верхнем купоне и проделав отверстие в нижней части минимум 3/16 дюйма или 5 мм. Если отверстие меньше 3/16 дюйма или 5 мм или сварной шов отходит от верхнего образца и остается внизу без отверстий, за исключением верхнего образца, это неисправность (Фото 9).) . Выполните этот сварной шов как в вертикальном, так и в потолочном положениях и испытайте его разрушающим методом (Фото 10) .
Сварка встык с подложкой
Это обычный сварной шов для структурного ремонта, и важно, чтобы он был выполнен правильно, поскольку это обычный шов для разрезания балки рамы, стойки или порога.
Для создания этого сварного шва требуется три образца: два верхних и один нижний. Разрыв между двумя верхними купонами имеет решающее значение. Если он будет слишком тугим, вы не добьетесь достаточного проникновения, чтобы добиться отрыва в нижнем купоне. Если она слишком широкая, верхние купоны отвалятся в процессе разрушения с небольшим проникновением в верхние купоны. Некоторые говорят, что зазор должен составлять от 2 до 4 толщин образца. Оставьте достаточно, чтобы добиться хорошего проникновения в нижний купон (Фото 11) .
Разметить и выполнить сварку. Сложите два верхних купона вместе (спина к спине). Зажав нижний купон в тисках, согните нижний купон в форме буквы «U», используя 3-фунтовые щипцы. молоток. Выньте нижний купон из тисков и крепко зажмите два верхних купона (Фото 12) .
С помощью большого долота и тяжелого молотка забейте U-образную подкладку вверх, вырвав металл из подложки и оставив его на сварном шве двух верхних купонов (Фото 13) . Вы должны оторвать не менее 1 дюйма металла от подложки (Фото 14) .