ЭЛЕКТРОХИМИЧЕСКАЯ ЗАЩИТА — это… Что такое ЭЛЕКТРОХИМИЧЕСКАЯ ЗАЩИТА?
металлов от коррозии, основана на зависимости скорости коррозии от электродного потенциала металла. В общем случае эта зависимость имеет сложный характер и подробно описана в ст. Коррозия металлов. В принципе, металл или сплав должен эксплуатироваться в той области потенциалов, где скорость его анодного растворения меньше нек-рого конструктивно допустимого предела, к-рый определяют, исходя из срока службы оборудования или допустимого уровня загрязнения технол. среды продуктами коррозии. Кроме того, должна быть мала вероятность локальных коррозионных повреждений. Это т. наз. потенциостатич. защита.
К собственно Э. з. относят катодную защиту, при к-рой потенциал металла специально сдвигают из области активного растворения в более отрицат. область относительно потенциала коррозии, и анодную защиту, при к-рой электродный потенциал сдвигают в положит. область до таких значений, когда на пов-сти металла образуются пассивирующие слои (см. Пассивность металлов).
Катодная защита. Сдвиг потенциала металла м. б. осуществлен с помощью внеш. источника постоянного тока (станции катодной защиты) или соединением с др. металлом, более электроотрицательным по своему электродному потенциалу (т. наз. протекторный анод). При этом пов-сть защищаемого образца (детали конструкции) становится эквипотенциальной и на всех ее участках протекают только катодные процессы, а анодные, обусловливающие коррозию, перенесены на вспомогат. электроды. Если, однако, сдвиг потенциала в отрицат. сторону превысит определенное значение, возможна т. наз. перезащита, связанная с выделением водорода, изменением состава приэлектродного слоя и др. явлениями, что может привести к ускорению коррозии. Катодную защиту, как правило, совмещают с нанесением защитных покрытий; необходимо учитывать возможность отслаивания покрытия.
Катодную защиту широко применяют для защиты от морской коррозии. Гражданские суда защищают с помощью А1-, Mg- или Zn-протекторных анодов, к-рые размещают вдоль корпуса и вблизи винтов и рулей.
Станции катодной защиты используют в тех случаях, когда требуется отключение защиты для устранения электрич. поля корабля, при этом потенциал обычно контролируют по хлорсеребряным электродам сравнения (х. с. э.). Критерием достаточности защиты является значение потенциала -0,75 В по х. с. э. или сдвиг от потенциала коррозии, составляющий 0,3 В (на практике обычно 0,05-0,2 В). Существуют автоматич. станции катодной защиты, расположенные на судне либо на берегу (при стоянке или ремонте). Аноды обычно изготовлены из платинированного титана, линейной или круглой формы, с околоанодными непроводящими экранами для улучшения распределения потенциала и плотности тока вдоль корпуса судна. Конструкция анодов обеспечивает их защиту от мех. повреждений (напр., в ледовых условиях).
Важное значение имеет Э. з. подземных сооружений в поле блуждающих токов, осн. причина возникновения таких токов — работа электротранспорта, реже — заземление электрооборудования. Борьба с коррозией в этих условиях сводится к контролю потенциала и установке дренажных устройств, обеспечивающих электрич. соединение источников токов утечки с защищаемым сооружением. Используют автоматич. дренажные устройства с включением и выключением в соответствии со значением защитного потенциала. Такие дренажные устройства обеспечивают надежную защиту вне зависимости от изменения знака потенциала на защищаемом сооружении.
Разрабатываются способы катодной защиты кузовов транспортной техники (автомобилей). Протекторные аноды используют для защиты отд. декоративных элементов кузова, при этом электронные устройства обеспечивают постоянный или импульсный ток; аноды, наклеиваемые на кузов, изготавливают из электропроводящего полимера (напр., графитопласта, углепластика) или нержавеющей стали. Для увеличения зоны действия защиты необходимо размещать аноды в наиб. коррозионноопасных точках или использовать электропроводящую окраску.
Анодная защита применяется в хим. и смежных с ней отраслях пром-сти в принципиально иных условиях, чем катодная защита; оба типа Э. з. в агрессивных средах дополняют друг друга. Металл конструкции или сооружения должен иметь область пассивности с достаточно низкой скоростью растворения, к-рая лимитируется не только разрушением металла, но и возможным загрязнением среды. Широко применяют анодную защиту для оборудования, работающего в серной к-те, средах на ее основе, водных р-рах аммиака и минер, удобрений, фосфорной к-те, в целлюлозно-бумажной пром-сти и ряде отд. произ-в (напр., роданида натрия). Особенно важна анодная защита теплообменного оборудования из легир. сталей в произ-ве серной к-ты; защита холодильников со стороны к-ты позволяет повысить рабочую т-ру, интенсифицировать теплообмен, повысить эксплуатац. надежность. Регулирование потенциала металла осуществляют автоматич. станциями анодной защиты (регуляторами потенциала), работающими с контролем потенциала и управляющим сигналом от электрода сравнения. Вспомогат. электроды изготавливают из высоколегир. сталей, кремнистого чугуна, платинированной латуни (бронзы) или меди. Электроды сравнения — выносные и погружные, близкие по составу к анионному составу агрессивной среды (сульфатно-ртутные, сульфатно-медные и т. п.). М. б. использованы любые электроды, имеющие в данной среде к.-л. устойчивый потенциал, напр. потенциал коррозии (электроды из чистого цинка) или потенциал электрохим. р-ции (осаждения покрытия, выделения хлора или кислорода). Зона действия защитных потенциалов зависит от области оптим. запассивированности металла и изменяется от неск. В (титановые сплавы) до неск. десятков мВ (нержавеющие стали при повышенных т-рах).
В злектрохим. произ-вах для защиты оборудования от токов утечки по электролиту устанавливают дополнит. электроды, устраняющие протекание тока через защищаемую пов-сть.
Лит.: Красноярский В. В., Электрохимический метод защиты металлов от коррозии, М., 1961; Фрейман Л. И., Макаров В. А., Брыксин Е. И., Потенциостатические методы в коррозионных исследованиях и электрохимической защите, Л., 1972; Люблинский Е. Я., Протекторная зашита морских судов и сооружений от коррозии, Л., 1979; Кузуб B. C., Анодная защита технологического оборудования, М., 1989.
В. А. Макаров.
Химическая энциклопедия. — М.: Советская энциклопедия. Под ред. И. Л. Кнунянца. 1988.
Электрохимическая защита трубопроводов | ЭХЗ-ЦЕНТР Москва

Сооружение электрохимической защиты трубопроводов предполагает выполнение комплекса работ.
Требуется проконтролировать коррозионное состояние подземных конструкций из металла, выполнить монтаж установок для электрохимзащиты, провести пусконаладочные работы, электроизмерительные работы в лабораторных условиях, а также доставить оборудование и материалы для ремонта ЭХЗ трубопроводов и их обслуживания.
Виды электрохимической защиты трубопроводов
Эффективным средством борьбы с коррозией металла выступают 2 вида электрохимической защиты:
- протекторная;
- катодная.
Протекторная основана на остановке процесса коррозии металлических конструкций под действием постоянного тока. Ее применяют вместе с защитными лакокрасочными покрытиями для продления срока их службы и обеспечения равномерного распределения электрического тока по поверхности металлоконструкций.
Катодная заключается в предохранении сооружений принудительной катодной поляризацией посредством внешнего источника постоянного тока. Отрицательный полюс такого источника подключают к защищаемому объекту, выполняющему роль катода. Чтобы получилась замкнутая по току цепь, полюс источника со знаком «плюс» подсоединяется к аноду. Тем самым сооружение отрицательно поляризуется, его потенциал сдвигается до показателя, при котором процесс коррозии металла сводится к нулю.
Монтажные работы
Монтаж подземных приборов контроля
Подземные приборы контроля требуется подключать, чтобы иметь возможность обнаружить повреждения в материалах строительства трубопроводов, не вскрывая поверхности грунта, а также чтобы определить глубину и расположение залегания трубопроводной трассы.
Монтаж стоек контрольно-измерительных пунктов
КИП разработаны для указания местоположения подземных трубопроводных трасс. С их помощью также контролируют электрохимическую защиту конструкций. Контрольно-измерительные пункты состоят из стойки и зафиксированного на ней терминала.
Монтаж анодных заземлителей
Глубинные заземлители защищают металлоконструкции, которые контактируют с водой и грунтом, сокращая случаи ремонта трубопроводов из материалов, подверженных коррозии. Используются в местах ограниченного землеотвода под анодное поле, на участках с низкой электропроводностью поверхностного грунтового слоя и в сложных районах залегания. Заземлители выполняются из ферросилидовых сплавов, благодаря чему достигается их стойкость к анодному растворению.
Монтаж станций катодной защиты
Станции катодной защиты — составляющие установок ЭХЗ. Широко применяются при эксплуатации нефтегазопроводов и стационарных нефтегазопромысловых сооружений, подземных помещений для хранения и скважин.
Пусконаладка
Пусконаладка включает в себя мероприятия по вводу смонтированного оборудования в эксплуатацию. Пусконаладочные работы проводят для выявления расхождений с проектом электроснабжения, настройки смонтированного оборудования и проверки готовности построенной системы к использованию. В результате их проведения обеспечивается бесперебойная работа оборудования в течение всего срока эксплуатации.
Мир современных материалов — Электрохимическая защита от коррозии
1. Изменение скорости коррозии под действием внешней ЭДС
Даже если омическое сопротивление пренебрежимо мало, существует предельное значение скорости коррозии, соответствующей току коррозии Iкорр. Этот предел определяется несколькими факторами. В частности, разностью потенциалов катода и анода, а также природой коррозионной среды. При очень большом омическом сопротивлении проблемы коррозии чаше всего не возникает. В этом случае никакой особой защиты не требуется. Однако, когда омическое сопротивление невелико, как это чаше всего и бывает, сильнее всего значение Iкорр определяется наклонами прямых Тафеля катода и анода, соответствующими их поляризационным сопротивлениям Rp.
Электрохимическая природа коррозии позволяет предложить способы сделать её быстрее, медленнее, и даже остановить почти полностью. По определению, в процессе коррозии происходит потеря электронов анодом, который при этом приобретает некоторый потенциал. Если повысить потенциал анода, наложив внешнюю ЭДС с помощью вспомогательного катода, помещенного в одну проводящую среду с анодом, как показано на рис. 1(a), следует ожидать, что скорость коррозии возрастет. Предложенный метод обычно используется при выполнении ускоренных коррозионных испытаний. При полном подавлении высвобождения электронов коррозия прекращается. Этот факт лежит в основе метода электрохимической катодной защиты.
Рис. 1. Влияние внешней ЭДС на скорость коррозии:
(а) ускоренная коррозия; б) катодная зашита
1 — испытываемый образец; 2 — изолирующее покрытие; 3 — пористое покрытие анода; 4 — коррозионная среда; 5 — вспомогательный катод.
Ясно, что и в том, и в другом случае необходим противоэлектрод (его ещё называют вспомогательным электродом), который замыкал бы электрическую цепь. Кроме того, для применения катодной зашиты, т е для образования электрохимической ячейки необходимо, чтобы среда, в которой металл подвергается коррозии, обладала хорошей электрической проводимостью. Поскольку при отсутствии проводимости нанесение изолирующего покрытия обеспечивает надлежащий уровень защиты, катодная защита рассматривается только в случае пребывания металла в проводящей среде. Примерами попадания металла в проводящую среду могут служить морские суда, морские платформы и буровые установки. В этих случаях применение катодной защиты оправдано. Метод, в котором используется вспомогательный анод, а ток возникает под действием внешней ЭДС, называется катодной зашитой с внешним наложенным током (англ. ICCP). Примерами применения этого метода могут служить системы ICCP транспортных трубопроводов, проложенных глубоко под землёй или пересекающих болотистую местность.
2. Растворимый анод.
Данный способ электрохимической защиты подразумевает наличие вспомогательного анода и внешнего источника ЭДС. Иногда использование внешнего источника затруднено. Например, в случае зашиты подвижных частей установки или корпуса морского судна. Тем не менее, катодная защита может быть достигнута и 6ез внешнего источника ЭДС. Для этого необходимо взять анод из материала, который стоит ниже защищаемого металла в ряду электрохимических напряжений. В этом случае растворение анода вызывает появление потенциала, которого может оказаться достаточно для подавления высвобождения электронов с поверхности защищаемой конструкции. Важно, чтобы и катод, и анод в гальваническом элементе, частью которого является защищаемый металл, были закреплены на движущейся конструкции. Так как анод в процессе такой зашиты постепенно растворяется, метол получил название коррозионной зашиты с растворимым анодом.
Хотя анод в подобных системах и находится в активном состоянии, существует естественный предел напряжения, которое способен развивать элемент. Предельной разности потенциалов в гальваническом элементе должно хватать, чтобы преодолеть омическое сопротивление электролита и поляризационное сопротивление электродов. Все это накладывает определённые рамки на протекающий через металлический провод, замыкающий элемент накоротко, ток. По этой причине системы катодной защиты с растворимым анодом оказываются предпочтительными в средах с высокой электрической проводимостью, например в морской воде.
В случае электрохимической защиты стали или других сплавов на основе железа растворимые аноды могут быть изготовлены из цинка, алюминия или магния.
Стандартный электродный потенциал цинка равен -0,760 В. Считая ионные активности цинка и железа одинаковыми, получаем 0,3 В для осуществления зашиты. Цинковые аноды не проявляют пассивности, поэтому можно использовать высокие плотности тока. Анодный выход по току в случае цинка высок. Распределение тока вдоль защищаемой конструкции такое же, как и в случае наложенного тока. Следовательно, из-за небольшой разности потенциалов и омического сопротивления электролита необходимо размещать аноды как можно ближе друг к другу. Применение цинковых анодов может оказаться неприемлемым в средах с высоким удельным сопротивлением, например в сухом грунте.
Стандартный потенциал алюминия составляет -0,85 В, что делает его более подходящим для анодной защиты металлом, чем цинк. Но поскольку оксидная пленка алюминия крайне пассивна, то алюминий довольно стоек к растворению. Для устранения этой проблемы алюминий легируют цинком, кадмием, оловом или индием. Кроме этого, малые добавки этих элементов снижают потенциал алюминия до -1,0 В.
Наиболее отрицательным стандартным потенциалом обладает магний, что делает его наиболее подходящим кандидатом для растворимых анодов. Чтобы избежать риска его пассивации при высокой плотности тока, его легируют, например, цинком.
3. Требования к напряжению.
Почти все катодные системы предназначены для коррозии конструкций из стали или других материалов на основе железа. Основным продуктом коррозии в этом случае является гидроксид железа (II). Принято считать, что для полной защиты железа необходим катодный потенциал 0,52 В.
Диаграммы коррозии показывают, что в катодно-контролируемых системах для защиты требуется более слабый ток. Это позволяет сэкономить мощность. Прикладываемое напряжение должно преодолевать поляризационное сопротивление электродов и омическое сопротивление среды. Площадь поверхности катода должна быть меньше площади анода. Катодные системы представляют собой хорошую защиту от тех видов коррозии, в которых площадь поверхности анодных центров невелика. Для примера можно назвать коррозионное растрескивание под напряжением и питтинг-коррозию.
Ток, необходимый для полной защиты конструкции, можно уменьшить нанесением антикоррозийного покрытия.
Подробности о роли защитных покрытий, расположении анодов и значениях тока, необходимого для электрохимической защиты стали в различных средах приведены в статье «Защита конструкций от коррозии».
4. Защитные покрытия
Площадь поверхности конструкции, которую необходимо защитить от коррозии, можно уменьшить, нанеся на неё антикоррозийное покрытие. Хотя нанесение антикоррозийного покрытия повышает плотность тока, общий ток, необходимый для защиты от коррозии, уменьшается. В случае нанесения покрытий воздействию коррозии подвергается только неокрашенная часть поверхности и пропуски. Прикладываемое напряжение защищает именно эти участки. Производство высококачественного покрытия без пропусков сопряжено с огромным повышением его стоимости. С другой стороны, катодная защита абсолютно незащищённой поверхности также экономически нецелесообразна. Таким образом, существует оптимальное сочетание обоих видов защиты от коррозии.
Со временем, по мере износа покрытия необходимо повышать значение тока для поддержания его защитных функций на необходимом уровне. Когда степень износа достигает предельной величины и повышение тока невозможно, то покрытие необходимо нанести заново.
Рис. 2. Возрастание тока при наличии покрытия, необходимого для электрохимической защиты, с течением времени.
В конце статьи приведем таблицу сравнения методов электрохимической защиты, их достоинства и недостатки.
Таблица 1. Сравнение методов электрохимической защиты [1].
Системы с растворимым анодом |
Системы с внешним источником тока |
Преимущества |
|
Нет необходимости в источнике тока |
Одна и та же система может быть использована дли защиты конструкций разных размеров |
Отсутствует риск «перезащиты», а с ним и водородного охрупчивания |
Можно использовать в средах с высокой удельной проводимостью |
Легко устанавливаются |
Легче управлять |
Недостатки |
|
Бесполезны в средах с высоким удельным сопротивлением |
Риск «перезащиты», как следствие водородное растрескивание и ослабление адгезии покрытий |
Фиксированный потенциал электрода вынуждает контролировать правильность размещения анодов |
Могут вызывать коррозию от блуждающих токов |
Требуются меры, направленные на смягчение процесса растворения. Может потребоваться добавление тех или иных легирующих элементов |
Стоимость содержания высока, хотя капитальные затраты относительно |
В море аппаратура может препятствовать движению судна, корпус которого она защищает от коррозии |
Системы требуют тщательного контроля. Контроль необходимо усиливать при смене времён года и условий внешней среды |
Капитальные затраты высоки, хотя стоимость содержания низкая |
|
Литература:
Р. Ангал. Коррозия и защита от коррозии. Изд-во «Интеллект», 2013. – 344 с.
Вас также может заинтересовать:
Что такое электрохимическая защита?
Что такое электрохимическая защита?
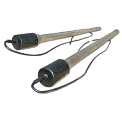
Электрохимическая защита – это эффективный способ защиты готовых изделий, конструкций и сооружений от электрохимической коррозии. Бывает, что в некоторых случаях возобновить защитный оберточный материал, лакокрасочное покрытие или же другое антикоррозионное покрытие невозможно, тогда целесообразно использовать электрохимическую защиту. Возобновлять антикоррозийное покрытие подземного трубопровода или же днища морского судна очень трудоемко и дорого, а иногда просто не представляется такая возможность. Электрохимическая защита надежно защищает изделие, конструкцию или сооружение от коррозии, предупреждая и останавливая разрушение подземных трубопроводов, днищ судов, различных резервуаров и т.п.
Электрохимическую защиту целесообразно применять в тех случаях, когда потенциал свободной коррозии находится в области интенсивного растворения основного металла либо когда идет интенсивное разрушение самой металлоконструкции (перепассивации). Для электрохимической защиты металлических конструкций и сооружений применяется множество различных средств.
Суть электрохимической защиты состоит в том, что к готовому металлическому изделию, конструкции или сооружению извне подключается постоянный ток (источник постоянного тока или протектор). Постоянный электрический ток на поверхности защищаемого изделия создает катодную поляризацию электродов микрогальванических пар. В результате катодной поляризации, бывшие анодными участки на поверхности металла, становятся катодными. А вследствие воздействия коррозионной среды идет разрушение не металла самой конструкции, а прикрепленного анода.
Таким образом, в зависимости от того, в какую сторону (положительную или отрицательную) смещается потенциал металла изделия или конструкции, электрохимическую защиту можно разделить на анодную и катодную.
При использовании анодной защиты, потенциал защищаемого металла смещается в более положительную сторону до тех пор, пока не будет достигнуто пассивное устойчивое состояние системы. При этом, достоинствами анодной электрохимической защиты является не только очень значительное замедление скорости коррозии, но также и тот факт, что в производимый продукт и среду не попадают продукты коррозии.
Катодная защита — является одним из основных видов защиты металлов от коррозии. Катодная защита, по сути, состоит в подключении к изделию внешнего тока от отрицательного полюса источника тока, который поляризует катодные участки коррозионных элементов, и благодаря этому приближает значение потенциала к анодному. Положительный полюс источника тока присоединяется к аноду. При этом антикоррозионная стойкость повышается, и коррозионные повреждения защищаемой конструкции практически сводятся к нулю. Анод же постепенно разрушается и его необходимо через некоторые интервалы времени заменять на новый.
Протекторная защита от коррозии | Мир инженера
Приветствую Вас, дорогие и уважаемые читатели сайта “world-engineer.ru”. Из этой статьи Вы узнаете, что такое электрохимзащита (ЭХЗ) и как электрохимическая защита от коррозии устроена, также узнаете, как устроена протекторная защита от коррозии трубопроводов о которой мы поговорим подробно.
Электрохимзащита (ЭХЗ расшифровка) разделяется на 4 вида:
1) Протекторная защита;
2) Катодная защита;
3) Электродренажная защита;
4) Анодная защита.
Схемы ЭХЗ трубопроводов
а) протекторная защита трубопроводов
б) катодная защита трубопроводов
в) электродренажная защита трубопроводов
1 – трубопровод;
2 – протектор;
3 – анодный заземлитель;
4 – выпрямитель переменного тока;
5 – рельсы электротранспорта.
Протекторная защита от коррозии – электрохимзащита трубопроводов с помощью тока гальванической пары. Принцип действия протекторной защиты заключается в защите стального защищаемого сооружения (это является катодом) при помощи электрохимического потенциала протекторных материалов (сплавы на основе магния, алюминия и цинка – аноды, некие “жертвенные” электроды), чей потенциал более электроотрицателен. Благодаря разности потенциалов в гальванической паре возникает ток, стекающий с анода (более электроотрицательного электрода) и натекающий из электролита на катод. Создание натекающего тока — цель электрохимической защиты от коррозии.
При разрушении анода-протектора его ионы уходят безвозвратно в землю, а освободившиеся электроны перетекают, как избыточные, на катод-трубопровод, заряжая его отрицательно. Т.е. под действием э.д.с. гальванопары “труба-протектор” в контуре “протектор — земля — трубопровод” возникает защитный ток, натекающий, как и положено при ЭХЗ, из земли на трубопровод. Вот такой принцип работы ЭХЗ.
Приведу пример расчета протекторной защиты трубопроводов одного из проектов тепловой сети.
Электрохимическая защита трубопроводов от коррозии
- Общие сведения
- Характеристики защищаемых подземных сооружений
- Расчет протекторной защиты трубопроводов
- Монтажные указания
- Монтаж протекторных установок
- Указания к пуско-наладочным работам
- Эксплуатация протекторных установок
- Мероприятия по охране труба
- Пожарная безопасность
- Мероприятия по обеспечению безопасности населения
1. Общие сведения
Рабочая документация по защите от электрохимической коррозии футляров тепловой сети под железнодорожным полотном на 10км 6ПК+50м станции Среднерогатская, разработан на комплекс работ по строительству объекта: «Реконструкция тепловой сети от ТК с восточной стороны дома №36 корп.4 по Пулковскому шоссе, до ТК на границе территории по адресу: Пулковское шоссе, д.30, литер В (2-й этап строительства)», выполнена в соответствии с требованиями следующих нормативных документов:
— ГОСТ 9.602-2016 «Единая система защиты от коррозии и старения. Сооружения подземные. Общие требования к защите от коррозии (ИУС 3-2017)»;
— «Инструкция по защите городских подземных трубопроводов от коррозии», РД 153-39.4-091-01, 2002г.
Рабочая документация соответствует строительным нормам и правилам, и другим нормативным документам, согласованным с Госгортехнадзором России.
Проектом предусматривается:
1) Прокладка 2-х стальных футляров 720х10 мм ГОСТ 10704-91 ст.3сп в ВУС изоляции по ГОСТ 9.602-89 тип 7 протяженностью 77,5 м методом ГНБ под железнодорожным полотном ОАО «РЖД».
2) Подземная прокладка в футлярах стальных трубопроводов тепловых сетей Т1, Т2 426х8/560 мм в заводской изоляции пенополиуретаном с защитным слоем из полиэтилена.
3) Обустройство 2-х тепловых камер вне полосы отвода железной дороги из сборного железобетона по Сер. 3.903 КЛ13 вып.1-3: ТК22, ТК23 с установкой запорной арматуры 2Ду400 мм для отключения участка теплосети и спускников 2Ду125 мм для опорожнения сети.
4) Обустройство 2-х неподвижных опор и сильфоных компенсационных узлов для компенсации температурного расширения.
Для электрохимзащиты (ЭХЗ) прокладываемых стальных футляров, проектом предусмотрено устройство узлов протекторной защиты от коррозии трубопроводов включая протектор магниевый ПМ-20У с установкой контрольно-измерительных пунктов.
2. Характеристики защищаемых подземных сооружений
№ п/п | Подземные сооружения | Изоляция, способ прокладки | Диаметр, мм | Длина, м |
1 | Футляр | Подземный | 720 | 77,5 |
2 | Футляр | Подземный | 720 | 77,5 |
3. Расчет протекторной защиты трубопроводов
Для защиты от электрохимической коррозии футляров настоящим проектом предусмотрена установка магниевых протекторов типа ПМ-20У, помещенных в мешки с активатором. Активатор предназначен для обеспечения равномерности растворения протектора и уменьшения сопротивления растеканию.
Размеры протектора — протектор магниевый ПМ-20У, мм
Тип анода | L | Н | а | r | Dl | Масса, кг, min |
ПМ-20У | 610±7 | 155±4 | 175±4 | 75±3 | 5±1 | 20 |
Размеры магниевых протекторов упакованных, мм
Тип анода | LА, min | Б | d | DПР | Масса, кг, min |
ПМ-20У | 710 | 50±3 | 206±4 | 270±5 | 60 |
1.Расчет протекторной защиты футляров.
Исходные данные: Длина футляра – LФ = 155 м; (2шт. по 77,5 м)
Диаметр футляра – dФ = 720 мм;
Глубина установки футляра — tФ = 4 м;
Футляр размещен в грунтах с средней коррозионной агрессивностью, в расчетах среднее удельное сопротивление грунта принимаем 31 Ом*м.
Расстояние протектора от трубопровода выбирают обычно равным 3…5 м, глубину заложения — на уровне трубопровода.
Определяем площадь поверхности футляра:
SФ = π*dФ*LФ = 3,14 * 0,72 * 155 = 350 м2;
Определяем ток необходимый для защиты футляра от коррозии:
IЗ = (ΔU/RИЗ,MIN)*SФ = (0,5/100)*350 = 1,752 А;
Определяем сопротивление футляра:
RФ = (ρ/2*π*LФ)*[ln (LФ2/dФ*tФ) + 0,5 ln (1 + (4*tФ2/ LФ2))] =
= (31 / 6,28*155) * [ln (24025/0,72*4) + 0,5 ln (1 + (4*16 / 24025))] = 0,288 Ом;
Определяем сопротивление протектора ПМ-20У:
RПР = (ρ/2*π*LА)*[ln (2LА2/DПР) + 0,5 ln ((4*tПР + LА) /(4*tПР — LА))] =
= (31 / 6,28*0,71) * [ln (1,42/0,27) + 0,5 ln ((4*3 + 0,71)/(4*3 — 0,71))] = 9,598 Ом;
где: LА — длина протектора, 0,71 м;
DПР — диаметр протектора 0,27 м;
tПР — глубина установки протектора, 2,5 м.
Определяем токоотдачу протектора ПМ-20У:
IПР = ΔU / (RПР + RФ1) = 0,9 / (9,598 + 0,288) = 0,091 А;
где: ΔU = UOD — UСТ = 1,6 — 0,7 = 0,9В — разность стационарных потенциалов между трубопроводом и магниевым протектором ПМ-20У;
Находим требуемое количество ПМ-20У протекторов:
N = IЗ / IПР = 1,752 / 0,091 = 20 шт.
В интернете есть программа расчета протекторной защиты — АРМ-ЭХЗ-6П, АРМ-ЭХЗ-7П, а также ElectriCS ECP электрохимзащита. Так что советую к использованию.
И самое важное. Необходимость установки протекторной защиты определяется отраслевыми регламентами и документами, по которым Вы работаете. Если согласно Вашей нормативной документации необходима защита, то делайте её. Для расчёта необходимо просто корректно ввести все исходные данные во все поля. Но для корректного расчёта необходим некий опыт и понимание того, что вы делаете, в вашем случае, необходимо знать электрифицированная данная ж/д или нет, есть ли блуждающие токи (а они скорее всего есть) и сами грунтовые условия (удельное сопротивление грунта). Возможно в Ваших условиях применение протекторов не возможно, и не целесообразно и нужна более серьёзная защита. Это всё зависит от необходимости и ответственности защищаемого сооружения.
4. Монтажные указания
Проектом предусмотрены узлы протекторной ЭХЗ трубопроводов подземных футляров, состоящих из протекторов магниевых ПМ-20У расположенных в скважинах, с выводами в контрольно-измерительный пункт в соответствии с планом расположения.
Контактное присоединение к футлярам выполнить без установки ковера.
При оборудовании контрольно-измерительного пункта неполяризующимся медносульфатным электродом сравнения длительного действия (ЭНЕС-1) с датчиком потенциала, устанавливают в КИП так, чтобы дно корпуса и датчик находились на уровне нижней образующей трубопровода и на расстоянии 100 мм от его боковой поверхности. При этом плоскость датчика должна быть перпендикулярна к оси трубопровода, а на боковой поверхности трубопровода не должно быть дефектов в изоляции.
Медносульфатные электроды сравнения после установки (так же, как контрольно-измерительные пункты, электроперемычки, контактные устройства, индикаторы коррозии и др.) необходимо засыпать вручную.
Монтажные указания по электрической схеме ЭХЗ трубопроводов
Узел ЭЗ-1:
- Установить проектируемый блок совместной защиты (БДРМ-10-2-22) на проектируемую стойку контрольно-измерительного пункта выносного типа;
- Установить протекторы типа ПМ-20У по чертежу ЭЗК—34.00 серия 5.905-32.07:
— в узле ЭЗ-1 в количестве 8 шт. вертикально в 4 — х скважинах глубиной 4,0 м;
- Для регулирования защитного тока и контроля защитного потенциала произвести подключение протекторов к стальным футлярам через контрольно-измерительный пункт с блоком совместной защиты (БДРМ-10-2-22) с установкой стального и медносульфатного электродов сравнения по чертежу ЭХ3.132 (альбом ДОАО “Газпроектинжиниринг”). Медносульфатный электрод сравнения длительного действия (ЭНЕС-ЗМ) устанавливается на специальную подушку из хорошо увлажненной глины, на уровне нижней образующей трубопровода. Рядом с ним установить стальной электрод сравнения из круга d=8 мм, L=1 м. Присоединение к трубопроводу выполнить по чертежу ЭЗК26.00 (серия 5.905-32.07 в.2).
- Электродренажные и контрольные кабели проложить в траншее на глубине 0,7 м от существующих отметок поверхности земли.
Узел ЭЗ-2:
- Установить проектируемый блок совместной защиты (БДРМ-10-2-22) на проектируемую стойку контрольно-измерительного пункта выносного типа;
- Установить ПМ-20У протекторы по чертежу ЭЗК—34.00 серия 5.905-32.07:
— в узле ЭЗ-2 в количестве 12 шт. вертикально в 6 -х скважинах глубиной 4,0 м;
- Для регулирования защитного тока и контроля защитного потенциала произвести подключение протекторов к стальным футлярам через контрольно-измерительный пункт с блоком совместной защиты (БДРМ-10-2-22) с установкой стального и медносульфатного электродов сравнения по чертежу ЭХ3.132 (альбом ДОАО “Газпроектинжиниринг”). Медносульфатный электрод сравнения длительного действия (ЭНЕС-ЗМ) устанавливается на специальную подушку из хорошо увлажненной глины, на уровне нижней образующей трубопровода. Рядом с ним установить стальной электрод сравнения из круга d=8 мм, L=1 м. Присоединение к трубопроводу выполнить по чертежу ЭЗК26.00 (серия 5.905-32.07 в.2).
- Электродренажные и контрольные кабели проложить в траншее на глубине 0,7 м от существующих отметок поверхности земли.
После выполнения СМР протекторной защиты необходимо произвести измерения электрических параметров с представителем специализированной организации:
— потенциал защищаемого сооружения до присоединения протекторов;
— разность потенциалов между защищаемыми сооружениями и протекторами до присоединения проводников;
— потенциал сооружения после подключения протекторной защиты;
— сила тока в цепи протектор — защищаемое сооружение;
Произвести ПНР протекторных установок.
5. Монтаж протекторных установок
При применении протекторов, не укомплектованных активатором, на монтажно-заготовительном участке следует предварительно зачистить поверхность протекторов, произвести спайку изолированных проводов с контактными сердечниками протекторов, место спайки тщательно изолируется и заливается слоем битума толщиной не менее 4 мм.
Монтаж протекторов ПМ-20У, упакованных в порошкообразном активаторе на заводе-изготовителе, выполняется в такой последовательности:
— с протекторов снимаются наружные мешки; протектор захватывается при помощи стальной 5-миллиметровой проволоки, загнутой на одном конце в виде крючка, за петлю хлопчатобумажного мешка и опускается в скважину или шурф;
— после равномерной засыпки протектора внутри скважины или шурфа мягким грунтом и послойной утрамбовки его монтажную проволоку вынимают;
— после удаления проволоки и закрепления протектора скважину досыпают грунтом и утрамбовывают с предосторожностями, необходимыми для сохранения протектора, соединительного провода и мест контакта провода с сердечником.
В сухих грунтах, при глубоком залегании грунтовых вод, после установки протектора и присыпки его грунтом в скважину заливают 2-3 ведра воды, после чего скважину полностью засыпают грунтом с послойной утрамбовкой. Допускается перед опусканием в скважину упакованного протектора окунуть его в бачок с водой для увлажнения после снятия внешнего бумажного мешка.
Перед приваркой контактных пластин, скоб или стержней к защищаемым сооружениям необходимо осмотреть состояние изоляции сооружений и в случае неудовлетворительного ее состояния известить об этом владельцев сооружений.
Контактные скобы и пластины присоединяют к действующим подземным сооружениям с помощью газо-, электро-, или термической сварки предприятиями, эксплуатирующими подземные сооружения.
6. Указания к пуско-наладочным работам
Проверка работы и промежуточная приемка протекторов осуществляется в течение 3-х суток после их монтажа, при этом производится измерение их электрических параметров.
Удовлетворительной считается работа протекторной установки, когда сдвиг потенциала на подземном сооружении при ее работе будет более чем на 0,2В в катодную сторону, а сила тока равна или близка расчетной.
Измерению подлежат следующие параметры установки:
— потенциал защищаемого сооружения до присоединения установки;
— потенциалы протекторов относительно земли до присоединения к защищаемым сооружениям;
— разность потенциалов между защищаемым сооружением и протекторами до присоединения проводников;
— потенциал сооружения после подключения протекторной защиты;
— сила тока в цепи «протектор — защищаемое сооружение».
Если при измерениях установлена неудовлетворительная работа протекторной установки, то необходимо определить причину неисправности и устранить ее. Основные показатели неудовлетворительной работы протекторов и ее причины, следующие:
— отсутствие электрического тока в цепи протектор-сооружение – обрыв проводников или нарушение контактных соединений;
— сила тока в цепи протектор — сооружение более чем на 50% меньше расчетной;
— плохое состояние контактов или неправильно смонтирован активатор.
7. Эксплуатация протекторных установок
При эксплуатации протекторных установок производят периодический технический осмотр, проверку эффективности.
Технический осмотр установок производят 2 раза в год. Контрольные измерения потенциалов на защищаемом сооружении производят 2 раза в год.
При проверке параметров установки протекторной (гальванической) защиты измеряют:
1) силу тока в цепи гальванический анод (ГА) — защищаемое сооружение;
2) разность потенциалов между ГА и сооружением;
3) потенциал сооружения в точке присоединения ГА при подключенном ГА.
Эффективность действия протекторной защиты определяют путем сравнения сдвига потенциала на защищаемом сооружении при контрольных замерах по отношению к пуско-наладочным значениям.
При ремонте и восстановлении протекторных установок должны производиться ревизия и осмотр всех скрытых контактных соединений.
Потенциалы протекторов, отключенных от сооружений, значения которых (по абсолютной величине) не ниже 1,2 В, характеризуют протекторы, как исправные.
8. Мероприятия по охране труда
При выполнении работ необходимо проводить мероприятия по организации безопасной работы с применением механизмов, транспортных средств и средств малой механизации.
До начала производства работ должна быть выполнена подготовка производства, включая проведение общих организационно-технических мероприятий, выполняемых в соответствии с действующей нормативно-технической документацией РФ и договором подряда.
До начала производства работ необходимо проверить все помещения на загазованность воздуха в них с помощью газоанализаторов взрывозащищенного исполнения. Места отборов проб воздуха определяются местной инструкцией. газоопасные работы должны выполняться под руководством и контролем руководителя работ. В процессе ее проведения все распоряжения выдаются только этим лицом.
При проведении газоопасных работ должны соблюдаться следующие правила:
— использование электрифицированных инструментов, дающих искрение, запрещается;
— инструмент должен быть из цветного металла, исключающего возможность искрообразования. Допускается использовать инструмент из черного металла, при этом его рабочая часть смазывается смазкой;
— в качестве переносного источника света должны использоваться светильники взрывозащищенного исполнения. Использование открытого огня в газоопасных местах запрещается;
— обувь персонала должна быть без стальных подковок и гвоздей.
Перед началом производства работ на всех дорогах, проездах должны быть поставлены предупредительные знаки и надписи, видимые в любое время суток, сделаны ограждения, указаны направления объездов и обходов. До начала производства работ необходимо установить ограждающие знаки, указывающие места расположения подземных коммуникаций. На ограждениях навешиваются надписи, запрещающие вход в огражденную зону («Осторожно. Опасная зона!»). Проходы и проезды в пределах опасной зоны должны иметь защитные навесы, боковые ограждения и надписи, запрещающие проход посторонним лицам.
При работах на высоте более 1,5 м и целесообразности устройства ограждений с целью предупреждения падения работающих необходимо пользоваться предохранительными поясами, без которых персонал не допускается на рабочее место и к ходовой лестнице.
В особо опасных местах необходимо пользоваться предохранительными поясами, имеющими по две цепи с карабинами для поочередного закрепления.
Запрещается работать, находиться на рабочем месте и пользоваться ходовой лестницей без защитных касок.
Подъемно-транспортные механизмы для приготовления материалов, склады и другие объекты, необходимые для работ, не должны находиться в опасной зоне.
Отклонения от проектной документации в процессе строительства, расширения, реконструкции, технического перевооружения, консервации и ликвидации опасного производственного объекта не допускаются.
При производстве всех видов строительно-монтажных работ необходимо соблюдать требования:
— СНиП 12-03-2001 «Безопасность труда в строительстве. Часть 1. Общие требования»;
— СНиП 12-04-2002 «Безопасность труда в строительстве. Часть 2. Строительное производство»;
— СанПиН 2.2.3.1384-03 «Гигиенические требования к организации строительного производства и строительных работ»;
— «Правила безопасности при работе с инструментом и приспособлениями»;
— ПОТ Р М-016-2001 «Межотраслевые правила по охране труда (Правила безопасности) при эксплуатации электроустановок».
9. Пожарная безопасность
При производстве работ должны соблюдаться «Правила пожарной безопасности в РФ».
Курение допускается только в специально отведенных местах. Места для курения должны иметь надпись -«Место для курения».
Первичные средства пожаротушения должны содержаться в исправном состоянии.
В местах производства работ на видных местах должны быть вывешены предупредительные плакаты о запрещении курения, применения открытого огня. На территории мазутного хозяйства курить, разводить огонь, пользоваться факелами, спичками, зажигалками, фонарями не во взрывобезопасном исполнении запрещается.
Все лесоматериалы, используемые для производства работ (леса, защитные козырьки, подмости и т.п.) должны быть обработаны специальным огнезащитным составом.
Ремонтная площадка должна быть обеспечена средствами пожаротушения -огнетушителями, кошма, ящиками с песком и лопатами.
Огневые работы (сварка, резка металла, варка битума) должны проводиться исключительно по наряду-допуску на огневые работы.
Строительно-монтажной организации оповестить руководство пожарной части, ответственной за данный район, о проведении работ и используемых горючих материалах.
10. Мероприятия по обеспечению безопасности населения
В целях создания безопасных условий для населения на период производства работ, а также оповещения граждан и предупреждения случаев травматизма и гибели людей, Заказчику разработать следующие мероприятия:
— установить в местах возможного скопления людей предупредительные знаки и плакаты о производстве работ;
— обеспечить видимое в любое время суток ограждение мест производства работ и опасных зон;
— при проведении работ выставить наблюдающих от подрядной организации для недопущения прохода граждан к опасной зоне;
Эвакуация населения на период производства работ не требуется.
Поделиться ссылкой:
Анодные заземлители: материалы, свойства и использование при электрохимической защите

- высокая электрохимическая устойчивость при анодной поляризации;
- высокая электропроводность;
- химическая стойкость к воздействию продуктов электролиза среды;
- сочетание достаточной прочности и пластичности;
- качество продукции;
- технологичность производства.
- растворимые;
- нерастворимые;
- малорастворимые.
Виды материалов для анодных заземлителей
Железо
Сплавы на основе железа относятся к растворимым материалам для АЗ. Анодное растворение железа проходит на скорости около 10 кг/(А • год). Такая высокая скорость растворения анодов — существенный минус, который не позволяет широко использовать сплавы на основе железа для системы катодной защиты. Кроме того, растворимые материалы имеют немало других отрицательных факторов. Например, при применении подобных АЗ грунтовые воды сильно загрязняются ионами железа. А из-за неэлектропроводности продуктов растворения такие аноды быстро выходят из строя.Графит

- высокое продольное сопротивление графита;
- отсутствие стойкости к влажности грунта;
- подверженность так называемому холодному горению;
- невысокая рабочая плотность тока.
Полимеры
Чтобы получить композицию полимерного электрода, производят пластификацию каучукоосновного связующего, а также вводят в смесь пластификатор и наполнитель, содержащий углерод. Полимерные аноды привлекательны с точки зрения стоимости, но имеют ряд существенных недостатков. Главный минус такой композиции в том, что электроды на основе подобных полимеров характеризуются высоким электрическим сопротивлением и низкими показателями максимально допустимого анодного тока. При повышении анодного тока электрод разогревается и на границе раздела фаз токоввод-полимерная электропроводная композиция образуется высокоомная оксидная пленка. В результате работа заземлителя полностью блокируется. Контактный узел электрода на основе полимеров по причине особенностей технологии производства невозможно выполнить при экструзии. Узел устанавливают в электрод, когда последний уже готов. Отсюда и недостатки:- невысокая механическая надежность;
- увеличенное переходное сопротивление контактного узла.
Ферросилид
Ферросилид — сплав железа с кремнием. Для анодов его используют при обычных плотностях тока с малыми потерями металла. Потери ферросилида варьируются в диапазоне 0,08-0,5 кг/(А • год). Устойчивость этого сплава против электрохимического разрушения объясняется тем, что на его поверхности образуется проводящая, сцепляющаяся пленка диоксида кремния. Пленка образуется в результате соединения ионов кремния с кислородом. Со временем она покрывает всю поверхность АЗ и не дает ионам железа выйти, за счет чего препятствует растворению анода. Поскольку процессы, протекающие на анодном заземлении, осуществляются с участием электронов, скорость их протекания зависит от величины стекающего, т.е. защитного тока. Железокремнистые анодные заземлители в условиях преимущественного выделения кислорода на аноде работают лучше, чем графитовые. Применение ферросилида в разных грунтах продемонстрировало его высокую эффективность как материала изготовления точечных заземлителей: как поверхностных, так и глубинных.Магнетит
Магнетит — перспективный материал для изготовления анодных заземлителей. Представляет собой сплав на основе оксидов железа. Магнетитовые изделия производят путем отливок при высокой температуре с использованием специальных добавок. Литой электрод получается гладким, плотным и твердым, напоминая стекло. Скорость растворения магнетита — 0,02 кг/(А•год). Анодное растворение магнетита проходит по такому же принципу, как у ферросилида, но есть несколько отличий. Магнетит обладает большей допустимостью плотности тока, поэтому подходит для широкого применения в различных грунтах и морской воде. Но у него как у материала для анодных заземлителей есть существенные недостатки: сложный технологический процесс и высокая стоимость конечных изделий.Платина и платинированные металлы

Вывод
Проектируя системы электрохимзащиты, нужно учитывать все плюсы и минусы материалов заземлителей. Лишь правильное понимание протекающих на АЗ процессов позволяет проектировщикам ЭХЗ грамотно подобрать анодный заземлитель в соответствии со свойствами материала и среды, в которой он будет работать в дальнейшем, а также дать верный прогноз по поводу периода эксплуатации.
|
ЭЛЕКТРОХИМИЧЕСКАЯ ЗАЩИТА
металлов
от коррозии, основана на зависимости скорости коррозии от электродного
потенциала металла. В общем случае эта зависимость имеет сложный характер
и подробно описана в ст. Коррозия металлов. В принципе, металл или
сплав должен эксплуатироваться в той области потенциалов, где скорость
его анодного растворения меньше нек-рого конструктивно допустимого
предела, к-рый определяют, исходя из срока службы оборудования или допустимого
уровня загрязнения технол. среды продуктами коррозии. Кроме того, должна
быть мала вероятность локальных коррозионных повреждений. Это т. наз. потенциостатич.
защита.
Катодная защита. Сдвиг потенциала
металла м. б. осуществлен с помощью внеш. источника постоянного тока (станции
катодной защиты) или соединением с др. металлом, более электроотрицательным
по своему электродному потенциалу (т. наз. протекторный анод). При этом
пов-сть защищаемого образца (детали конструкции) становится эквипотенциальной
и на всех ее участках протекают только катодные процессы, а анодные, обусловливающие
коррозию, перенесены на вспомогат. электроды. Если, однако, сдвиг потенциала
в отрицат. сторону превысит определенное значение, возможна т. наз. перезащита,
связанная с выделением водорода, изменением состава приэлектродного слоя
и др. явлениями, что может привести к ускорению коррозии. Катодную защиту,
как правило, совмещают с нанесением защитных покрытий; необходимо учитывать
возможность отслаивания покрытия.
Широко распространена катодная защита подземных сооружений. Практически все магистральные и городские трубопроводы, кабели, подземные хранилища и скважины, особенно в засоленных грунтах, снабжены устройствами для катодной защиты в сочетании с защитными покрытиями. Как правило, электрохимическая защита осуществляется от станций катодной защиты, протекторные аноды применяют лишь при отсутствии источников тока. Потенциал сооружения контролируют по сульфатно-медным электродам сравнения; ток катодной защиты периодически регулируют, исходя из потенциала защиты в разл. точках сооружения. По мере разрушения защитного покрытия ток защиты увеличивают. Протекторные аноды м. б. изготовлены из железокремниевых сплавов или графитопластов, снабжаются околоанодной засыпкой (кокс, уголь) для снижения общего сопротивления растеканию тока с анода в землю. По мере удаления анода от защищаемого сооружения увеличивают необходимое напряжение защиты (обычно до 48 В, для сильно удаленных анодов до 200 В), при этом улучшается распределение защитного тока. Для защиты разветвленных городских сетей или для совместной защиты неск. сооружений применяют глубинные аноды, расположенные под землей на глубине 50-150 м. Важное значение имеет электрохимическая защита подземных сооружений в поле блуждающих токов, осн. причина возникновения таких токов — работа электротранспорта, реже — заземление электрооборудования. Борьба с коррозией в этих условиях сводится к контролю потенциала и установке дренажных устройств, обеспечивающих электрич. соединение источников токов утечки с защищаемым сооружением. Используют автоматич. дренажные устройства с включением и выключением в соответствии со значением защитного потенциала. Такие дренажные устройства обеспечивают надежную защиту вне зависимости от изменения знака потенциала на защищаемом сооружении. Катодную защиту стальной арматуры в железобетоне применяют для свай, фундаментов, дорожных сооружений (в т. ч. горизонтальных покрытий) и зданий. Арматура, сваренная, как правило, в единую электрич. систему, корродирует при проникновении в бетон влаги и хлоридов. Последние могут попадать в результате воздействия морской воды или использования солей-антиобледенителей дорожных сооружений, применения хлоридов для ускорения твердения бетона. Весьма эффективна санация бетона старых зданий с установкой катодной защиты. При этом устанавливают первичные аноды из кремнистого чугуна, платинированных титана или ниобия, графита, титана с металлооксидным покрытием, к-рые обеспечивают подвод тока к вторичным (распределительным) анодам (титановой сетке с металлооксидным покрытием или электропроводящим неметаллич. покрытием, титановому стержню с покрытием), расположенным вдоль всей пов-сти сооружения и закрытым сверху относительно тонким слоем бетона. Потенциал арматуры регулируют, изменяя внеш. ток. Разрабатываются способы катодной защиты кузовов транспортной техники (автомобилей). Протекторные аноды используют для защиты отд. декоративных элементов кузова, при этом электронные устройства обеспечивают постоянный или импульсный ток; аноды, наклеиваемые на кузов, изготавливают из электропроводящего полимера (напр., графитопласта, углепластика) или нержавеющей стали. Для увеличения зоны действия защиты необходимо размещать аноды в наиб. коррозионноопасных точках или использовать электропроводящую окраску. Анодная защита применяется в хим.
и смежных с ней отраслях пром-сти в принципиально иных условиях, чем катодная
защита; оба типа электрохимической защиты в агрессивных средах дополняют друг друга. Металл
конструкции или сооружения должен иметь область пассивности с достаточно
низкой скоростью растворения, к-рая лимитируется не только разрушением
металла, но и возможным загрязнением среды. Широко применяют анодную защиту
для оборудования, работающего в серной к-те, средах на ее основе, водных
р-рах аммиака и минер, удобрений, фосфорной к-те, в целлюлозно-бумажной
пром-сти и ряде отд. произ-в (напр., роданида натрия). Особенно важна анодная
защита теплообменного оборудования из легир. сталей в произ-ве серной к-ты;
защита холодильников со стороны к-ты позволяет повысить рабочую т-ру, интенсифицировать
теплообмен, повысить эксплуатац. надежность. Регулирование потенциала металла
осуществляют автоматич. станциями анодной защиты (регуляторами потенциала),
работающими с контролем потенциала и управляющим сигналом от электрода
сравнения. Вспомогат. электроды изготавливают из высоколегир. сталей, кремнистого
чугуна, платинированной латуни (бронзы) или меди. Электроды сравнения -
выносные и погружные, близкие по составу к анионному составу агрессивной
среды (сульфатно-ртутные, сульфатно-медные и т. п.). М. б. использованы
любые электроды, имеющие в данной среде к.-л. устойчивый потенциал, напр.
потенциал коррозии (электроды из чистого цинка) или потенциал электрохим.
р-ции (осаждения покрытия, выделения хлора или кислорода). Зона действия
защитных потенциалов зависит от области оптим. запассивированности металла
и изменяется от неск. В (титановые сплавы) до неск. десятков мВ (нержавеющие
стали при повышенных т-рах).
Лит.: Красноярский В. В., Электрохимический метод защиты металлов от коррозии, М., 1961; Фрейман Л.И., Макаров В.А., Брыксин Е. И., Потенциостатические методы в коррозионных исследованиях и электрохимической защите, Л., 1972; Люблинский Е. Я., Протекторная зашита морских судов и сооружений от коррозии, Л., 1979; Кузуб B. C., Анодная защита технологического оборудования, М., 1989. В. А. Макаров.
|